MRPで発生する異常と対処
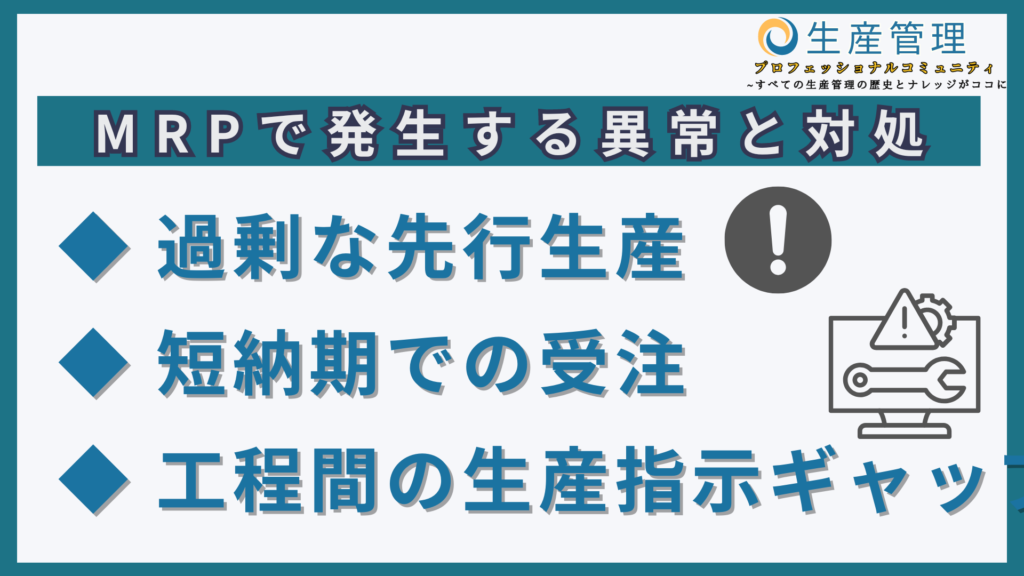
今回はMRPの過程における、
異常な状態と必要な対処方法について
いくつか紹介していきます。
目的の無い過剰な先行生産
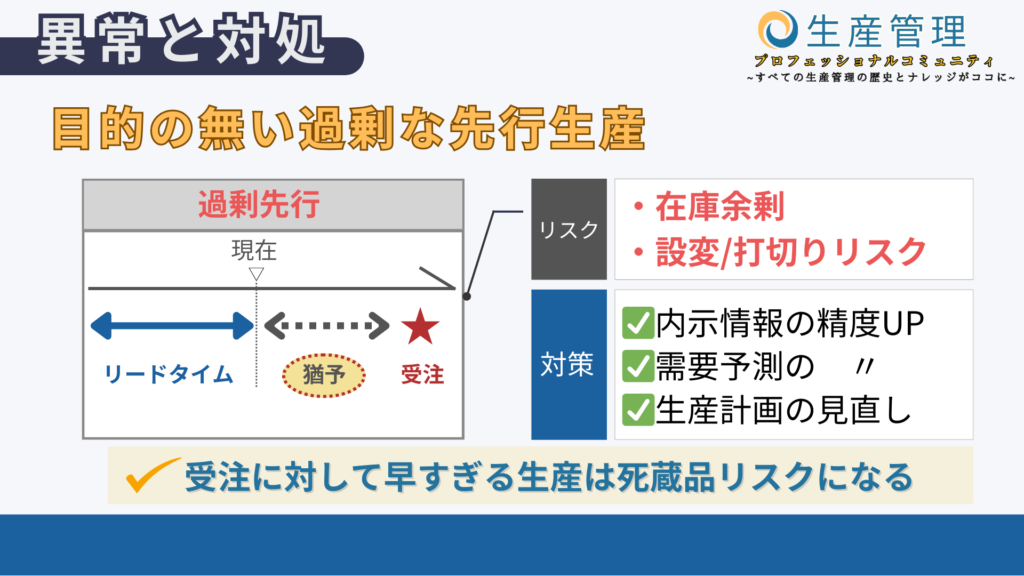
まずは、過剰な先行生産です。
これは、先にある、内示や受注に対して早く作りすぎてしまった場合です。
早く作れば安心と思うかもしれませんが、
その分の在庫スペースが必要になってしまったり、
その間に、もしキャンセルや設計変更、
打ち切りなどが発生した場合、その製品はムダになってしまいます。
出来る限り、先々の情報の精度を上げたり、
納期までひきつけて生産計画を立てていくことで防いでいきましょう。
短納期での受注
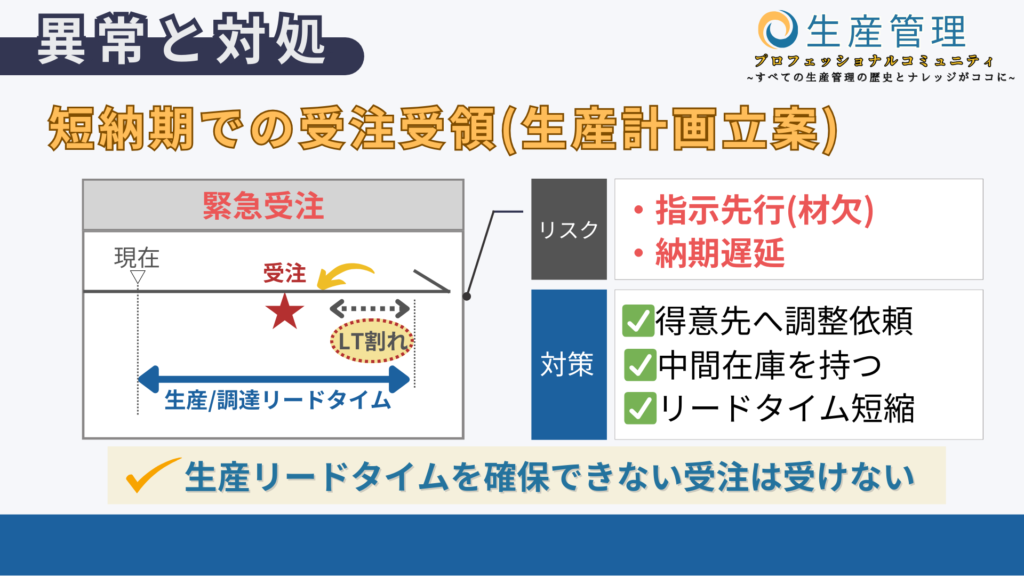
そして次が、短納期での受注が来てしまって、
リードタイムの確保ができない状況です。
生産するためには10日必要なのにもかかわらず、
5日後に納入してほしいというオーダーを受けたような状況です。
当然、このまま各工程に指示を出してしまっていては、
成り立たないだけではなく、納期に間に合わないことは想像ができるかと思います。
短期的な対応としては、きちんと得意先へ状況を説明して調整してもらったり、
各工程に依頼をして、前倒して緊急対応をしてもらうかになると思います。
また、今後に備えての対応としては、
在庫を確保しておくか、手配のリードタイムを短くできないか検討していくことも重要です。
工程間の生産指示ギャップ
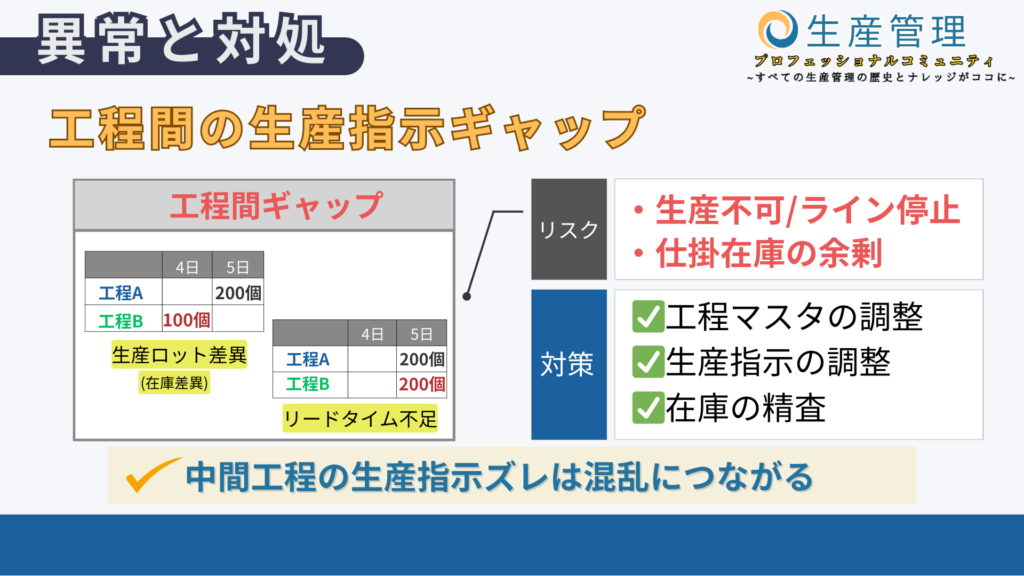
そして、MRPによる、各工程の管理をする上で、
一番の難しさとも言える問題が、工程間の様々なギャップです。
後工程である工程Aと前工程である工程Bの指示数が違っていたり、
リードタイムが確保されていないような
指示の出し方がされている、といったギャップが発生する場合です。
当然、計画通りに生産できなかったり、
余計な在庫が発生することにもつながります。
これは、生産ロットやリードタイムの設定をする工程マスタが間違っていたり、
帳簿上、システム上の在庫数が間違っているなどの原因が考えられます。
各工程のマスタの整備や、在庫精度の向上がなければ、
MRPによる管理が逆に混乱のもとになってしまうので、注意していきましょう
おわりに
今回は、MRPについて解説をしていきました。
多くの製造現場で使用されているものの、
適切に扱っていくことは意外と難しく、
苦労している人も多いのではないでしょうか。
ぜひ、しっかりと理解をして、
MRPに振り回されることなく、
上手に使える人材になっていきましょう。
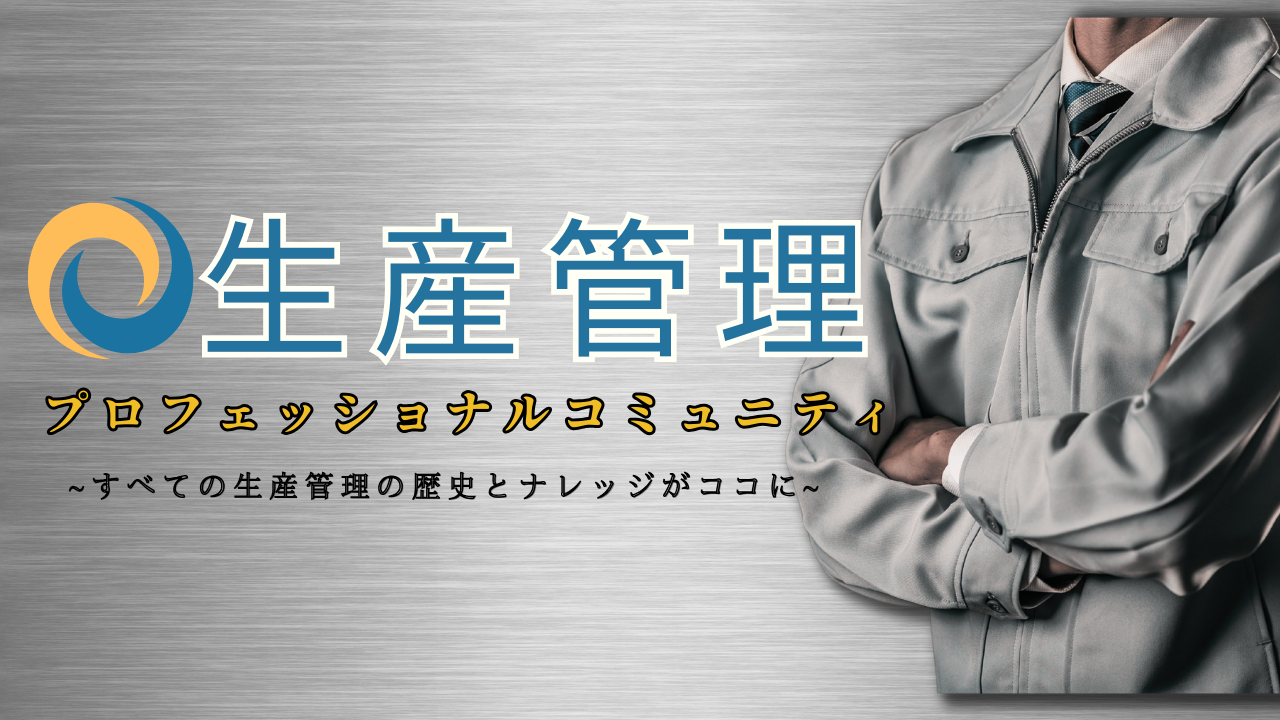
コチラのコラム記事は
ほんの一部分に過ぎません!
『生産管理プロフェッショナルコミュニティ』に入会すれば...
✅すべての教材テキストを見放題!
✅疑問・質問・悩みをいつでも相談し放題!
✅生産管理の精鋭と交流でき、成長し放題!