棚卸しのすべて
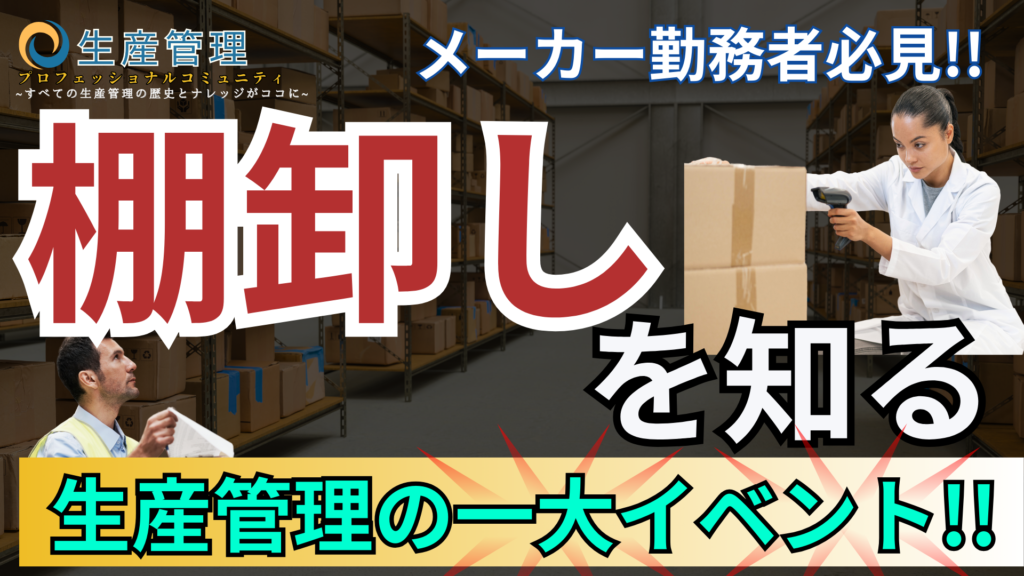
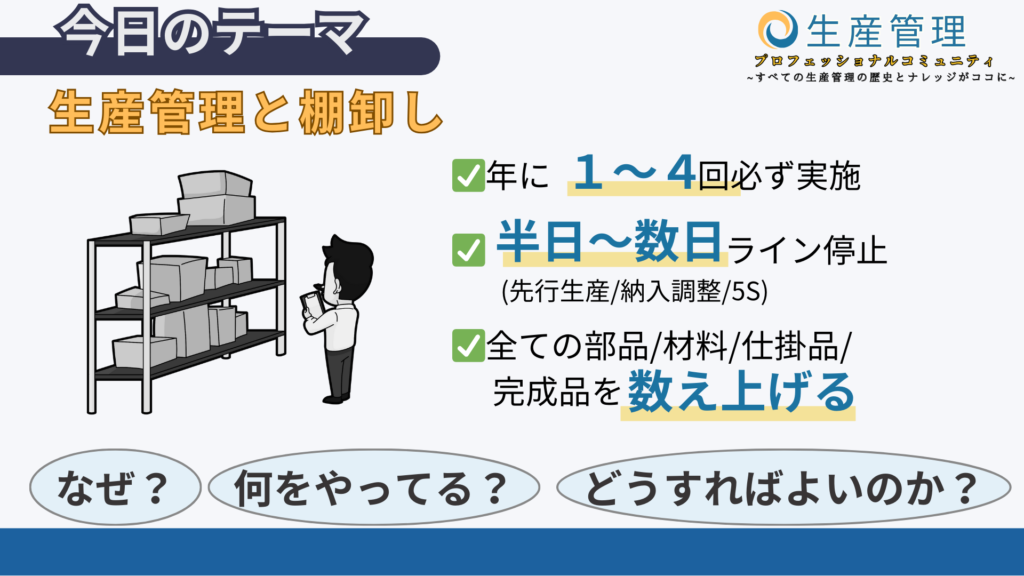
「棚卸し」と聞いて、どのようなイメージをもつでしょうか。
生産管理にとって最大のイベントとも言える棚卸は、
会社によっては4半期に一回、半年に1回、年に一回実施され、
場合によっては丸っと数日間生産ラインを停めて行うような工場もあるでしょう。
その際には先行生産や納入量の調整をしたり、5Sの再徹底に伴い、
特に忙しいイメージを持たれている生産管理の人も多いのではないでしょうか。
棚卸しの際には工場内にあるすべての部品から完成品まで、
全員総出で数え上げる姿が見られ、工場の中はいつもと違う雰囲気に包まれてます。
一体なぜ、ここまで大がかりなことをしなければいけないのか、
棚卸しでは、何が行われているのか、簡単に終わらせる方法はないのか、
毎年必ずやっているにもかからず、年に1,2回だから…
といってなかなか効率化が進んでいない工場も多いのではないでしょうか。
今回は、製造業における棚卸しについて掘り下げていきたいと思います。
目次
棚卸しの目的
一体何のために棚卸しなんていう、面倒なことを行うのか理解できていますか?
実は、会計上の理由と在庫管理上の理由があるんです。
順にみていきましょう。
◆会計処理上の重要性
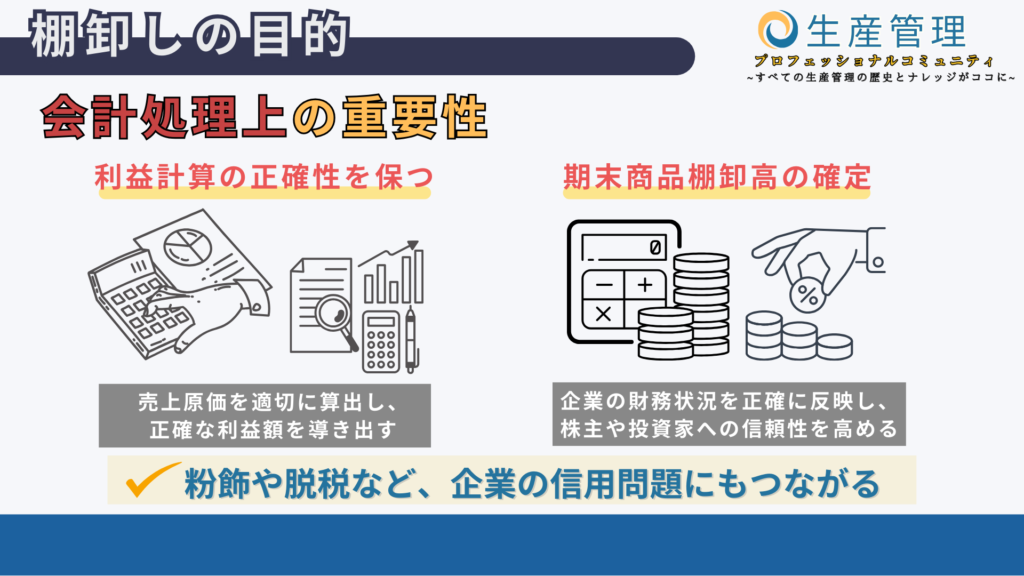
会計上の目的の一つとして
利益計算の正確性を保つことが挙げられます。
在庫を正確に評価することによって、
売上原価を適切に算出し、正確な利益額を導き出すことに繋がります。
経営戦略を立てていくためには、棚卸による正確な現状把握が重要なんです。
そして次は、
決算に必要な期末商品棚卸高の確定です。
決算報告や税務申告に向けて、
企業の財務状況を正確に反映し、
株主や投資家への信頼性を高めることにつながるわけです。
棚卸しをおろそかにしてしまうと、
粉飾や脱税など、企業の信用問題へとつながる
非常に重要な位置づけになっているんです。
◆在庫管理上の重要性
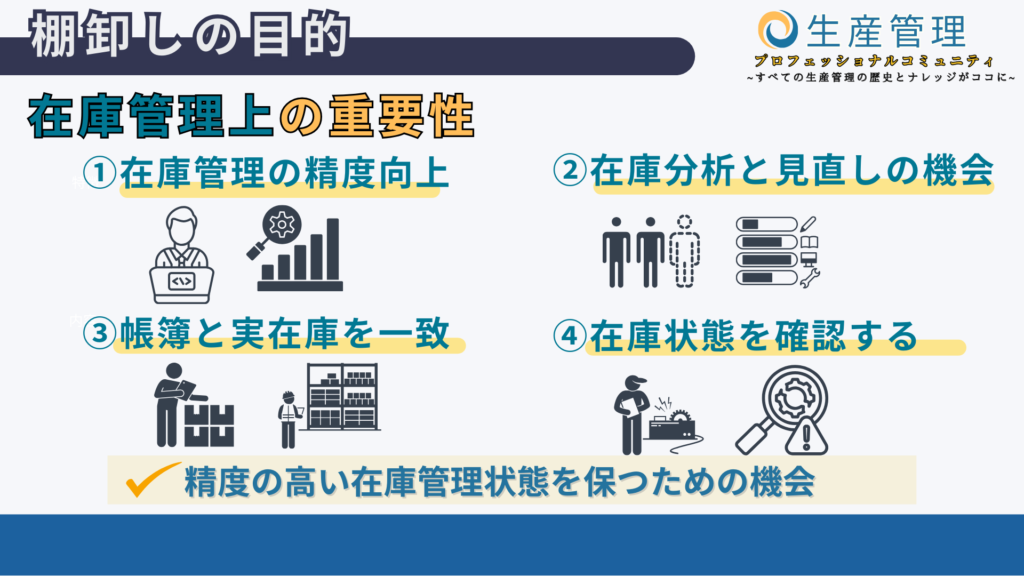
生産管理が適切な在庫管理をする上でも大事な目的がいくつかあるんです。
まずは、在庫の精度を向上させるということです。
棚卸しは、工場内外に
何が、どこに、どれだけあるのか再確認するタイミングなんです。
あるべき場所にあるべきものが本当にあるのかどうか確かめる機会になるわけです。
そして次が、在庫の分析と見直しの機会としての重要性です。
今の在庫状況が適切かどうか、
過剰な在庫や不足している部分があるかどうか、
ABC分析や在庫回転率などによって、
在庫状況の見直しの機会として、もってこいのタイミングなんです。
他にも、帳簿と実在庫を一致させるという目的もあります。
帳簿上の在庫数と実際の在庫数が一致していなければ、
生産管理はできません。
棚卸のタイミングを基準として
帳簿在庫と実在庫の一致させる処理をすることによって、
潜在的な異常やリスクを洗いだせるわkです。
そして最後が、在庫状態を確認するということ。
棚卸しを行うことで、
・部材の破損や劣化
・賞味期限切れなど
在庫の品質面の状態を確認して、
売れないモノや使えないものは、このタイミングで廃却する工場も多いでしょう。
棚卸しの種類
一口に棚卸といっても、さまざまな種類があります。
まずは、カウントをするかどうかによって、分類されます。
◆実地棚卸と帳簿棚卸
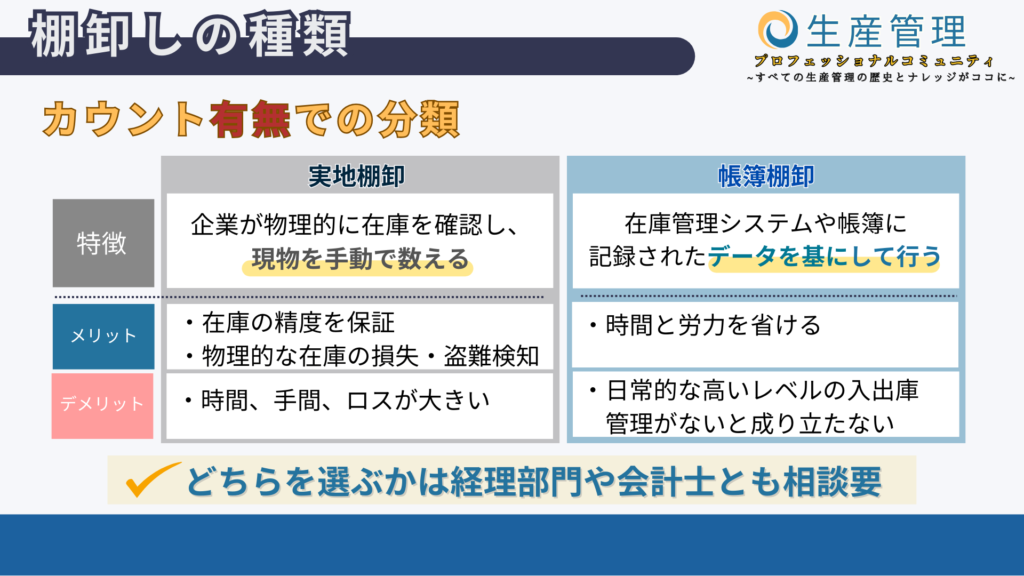
製造業における一般的な棚卸は実地棚卸と呼ばれるものです。
これは、実際に現場にある在庫を確認し、現物を手動で数えるものです。
当然、現地で一転一転確認するので、在庫の精度を保証し、
その異常にも気づきやすいというメリットがある反面、
時間や労力がかなり必要になるため、計画的に実施する必要があります。
それに対して、在庫管理システムや
帳簿に記録されたデータをもとに行うことを帳簿棚卸と呼びます。
物理的にカウントするのではなく、
記録されたデータが正しいものとして、在庫を評価します。
この方法は時間と労力を省くことはできますが、
データの正確性に大きく依存するため、
定期的な確認と更新、日常的な高いレベルの入出庫管理ができていなければ、
成り立たない棚卸とも言えます。
この2つについて、どちらを選ぶべきかは、
現場の一存だけ決めることではなく、
経理部門や会計士などと相談して、慎重に選択していく必要があります。
◆一斉棚卸と循環棚卸
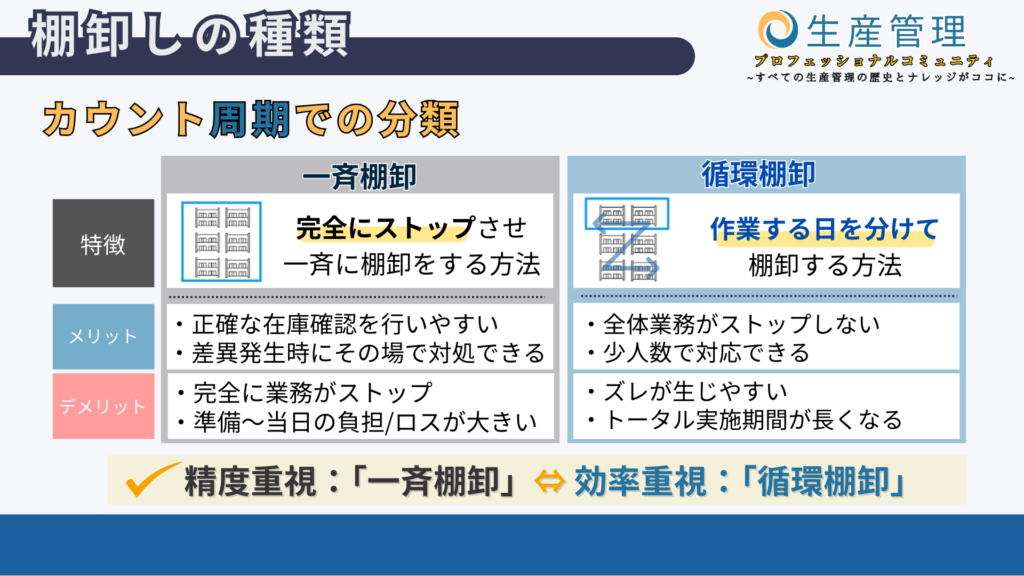
そして次は、カウントをする実地棚卸の中でも、
そのタイミングや頻度によって、分類されます。
まずは一斉棚卸です。
工場における生産や入出荷業務を全てストップさせて、
一斉に数え上げる方法です。
全てを停止させて確認作業を行うので、
正確に在庫確認ができたり、
何か異常があっても、
その場で対処できるという利点はありますが、
数時間から長ければ、
数日間にわたり、完全に業務を停めるということは、
当日だけではなく、そのための準備にかかる部分も合わせて、
大きな負担、ロスが発生してしまうのが、欠点です。
それに対するものとして、循環棚卸というものがあります。
これは、すべての在庫を一度に調べるのではなく、
在庫の種類や場所、作業する日を分けて棚卸する方法です。
循環棚卸であれば、
工場全体を停める必要はなく、並行してカウント作業を行えます。
さらに、一度に大量の在庫数をカウントする必要がないため、
少人数で対応できることもメリットの1つです。
ただその反面、棚卸前後で動きがあるので、
精度の担保がしづらかったり、計画的に実施しないと
トータルでかかる期間が長くなってしまう可能性もあります。
精度重視なら一斉棚卸、効率重視なら循環棚卸という選択になってくるでしょう。
棚卸しのカウント方法
◆伝票方式(タグ方式)
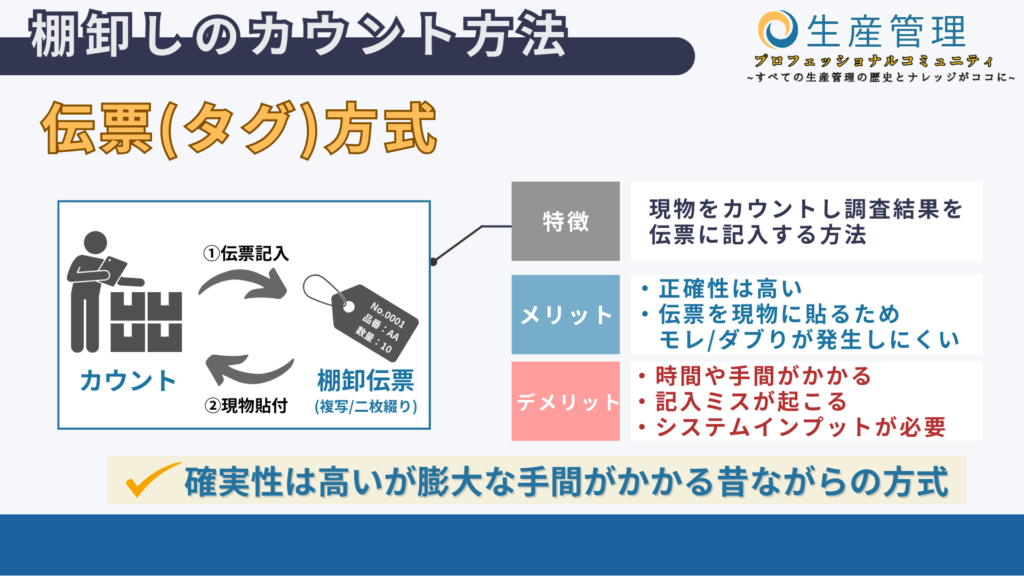
ここからは実際にカウントや集計方法について解説をしていきます。
まずは、伝票方式という形があります。
これは、現物をカウントして、
その結果を棚卸伝票、棚卸現品票、棚札などと呼ばれるものに記入していく方法です。
この伝票は連番管理がされていることが多く、
全て回収したかどうかの管理、不正や混入を防ぐことができ、正確性は高いです。
また、複写式のものや上下で切り離せるものを使用して、
カウントした現物や棚には、その伝票を貼り付けていくことで、
その在庫はカウント済であることが分かりやすく、モレやダブりを防ぐ効果があります。
ただ、記入による手間やミスも発生しやすく、
棚卸後にシステムに伝票結果を入力する必要もあるので、膨大な工数がかかってくるわけです。
多くの製造現場で採用されているこの方法は、
確実に行える反面、手間がかかってしまう昔ながらの方法と言えるでしょう。
◆リスト方式
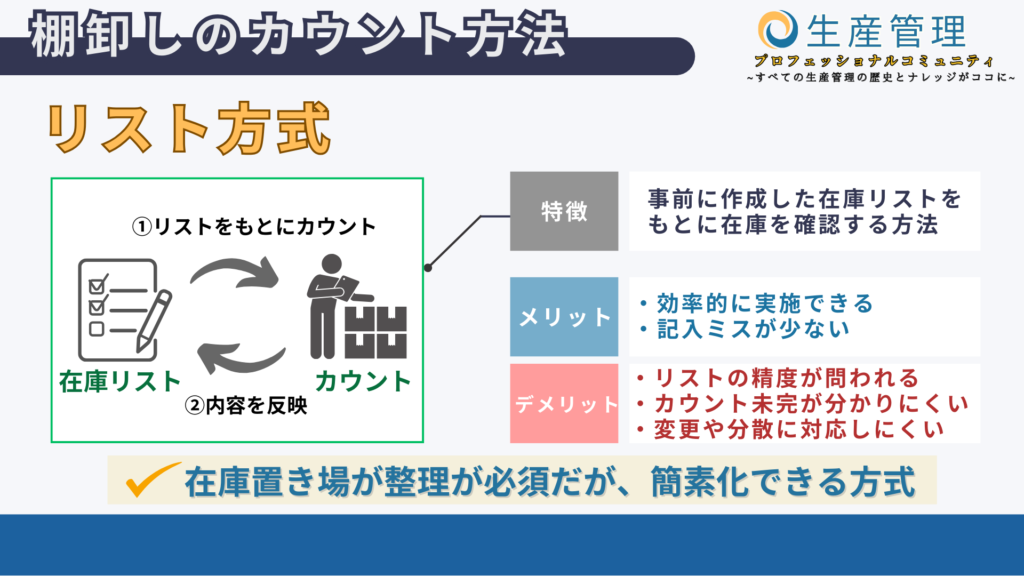
続いては、リスト方式と呼ばれるものです。
リスト方式は、事前に作成した在庫リストに基づいて、個々の製品を確認していく方法です。
この方式では、リストに記載されたアイテムごとに、
実際の在庫数をカウントし、リストと照らし合わせます。
伝票を使うよりは、効率的に実施でき、
数量を確認して記入するだけなので、
比較的記入ミスは防げるでしょう、
ただ、事前に作成する在庫リスト、棚卸リストの精度が悪ければ混乱しますし、
現物に印をつけるなどして、終わったものかどうかも明確する工夫も必要です。
また、急に置き場所が変わるとリストの更新が間に合わなかったり、
同じエリアに同じものが点在しているようなケースだと逆に確認がしづらくなるので、注意しましょう。
事前の準備さえ上手くできれば、効率的に実施できる方法がこのリスト方式なんです。
◆各種ツール活用 (QR/RFID/重力センサー/AI)
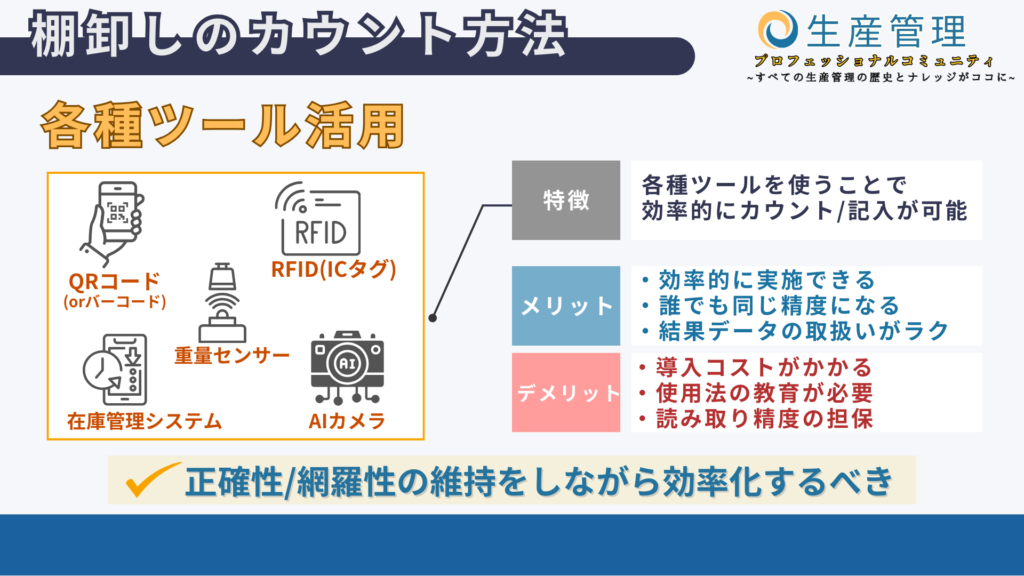
他にも、今ではさまざまな便利なツールがあるので、紹介していきます。
例えば、QRコードを読み取る方法は、もはや一般的に広まっています。
RFID技術によって、一括読み取りができたり、
在庫管理システムの進化に伴い効率化も進んでいます。
他にも重量センサーやAIの画像認識によって、
人が一つ一つ数える必要はなくなってきています。
当然、これらを活用すれば、効率的で、ヒューマンエラーも防げて、
誰がやっても同じような結果を出すことができます。
棚卸結果はデータとして残るので集計作業も効率化できるでしょう。
ただ、導入コストがかかったり、ツールを正しく使うための教育は必須です。
また、RFIDの一括読みとりやAIの精度を鵜吞みにするのではなく、
その結果が、なぜ正しいと言えるのか、精度はどのレベルにあるのか、
説明できるようにしておくべきでしょう。
棚卸における正確性と網羅性を維持することが大前提なので、
効率化する際は気を付けていきましょう。
業界別の棚卸し方法
続いて、棚卸の特徴や注意点を業界別に紹介していきます。
◆製造業(工場)
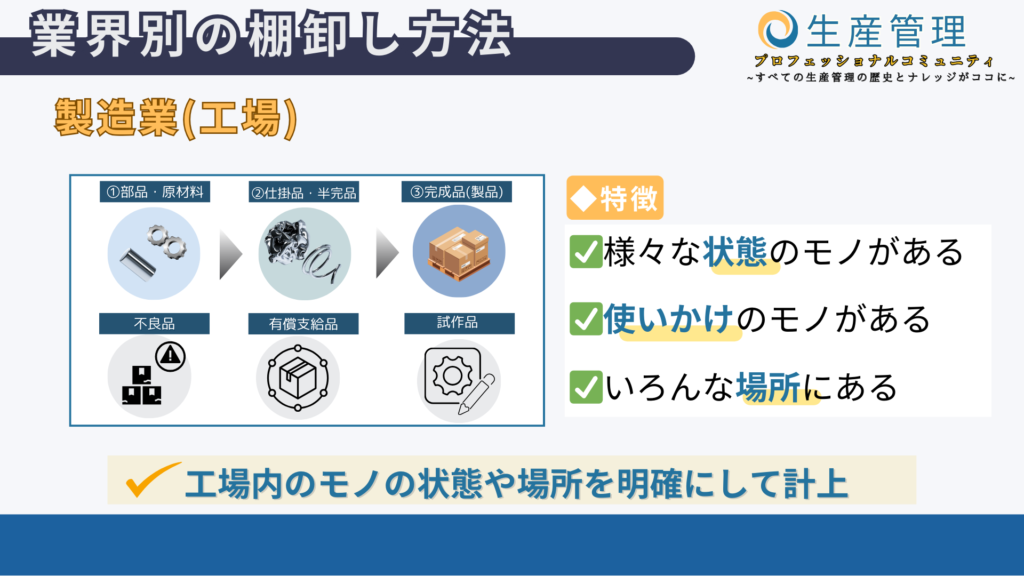
製造業の特徴は、工場の中で、状態が変わるということにあります。
部品や材料が、仕掛品になり、完成品になります。
他にも、不良品や支給品、試作品など、同じものでも、
それがどういった状態のものなのかに、注意して棚卸をしていく必要があります。
他にも、使いかけのモノがあったり、同じものがさまざまな場所で使われていたりするので、
何が、どこに、どれだけ、どういった状態であるのか明確にしながら棚卸をしていかなければいけない、
ということを押さえておきましょう。
◆小売り(店舗)・倉庫(卸)
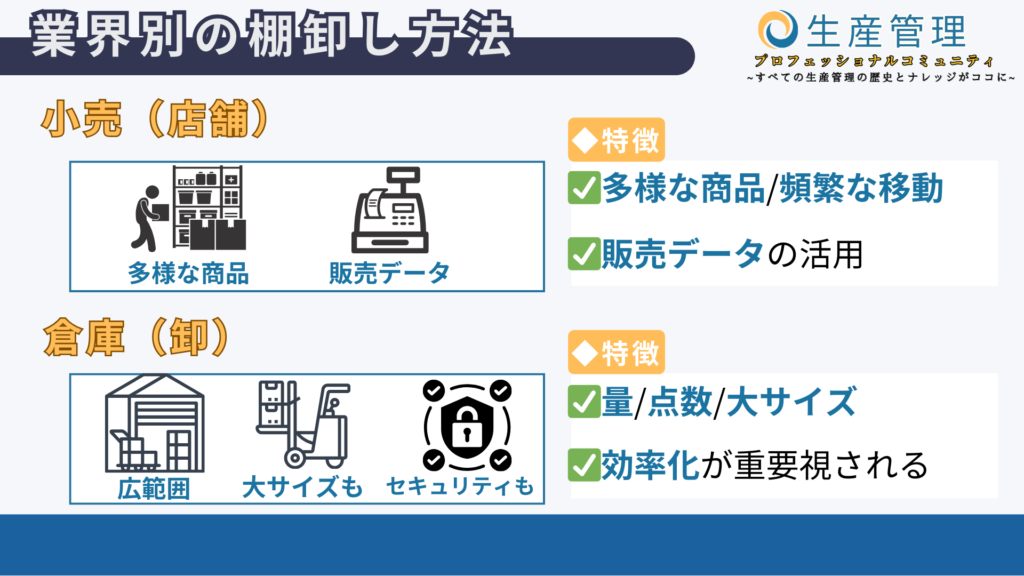
これが、スーパーやコンビニなどの小売店舗の場合は、商品のレパートリーも多く、
頻繁にレイアウトや置き場所も変わってくるのが特徴です。
必ずレジを通すので販売データと照合しながら実施するのが一般的です。
倉庫や卸センターの場合は、
巨大な倉庫に膨大な量や点数の商品があるので、
効率的に実施することが求められます。
いろんな会社から預かっているモノも多いので、
セキュリティや品質管理のも気を付ける必要があるのも倉庫の特徴です。
よくあるミスと対策ポイント
◆棚卸差異率
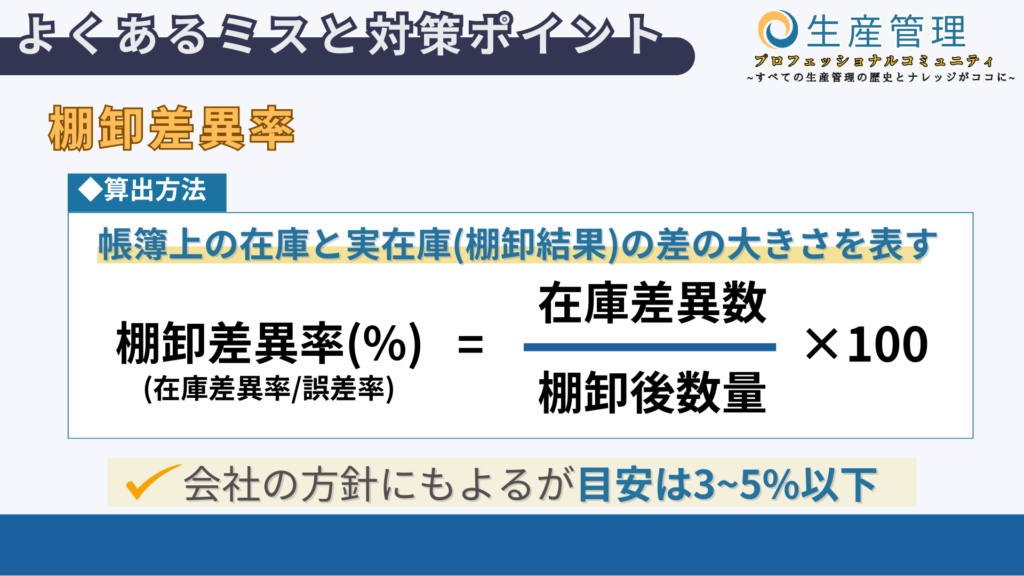
ここで、棚卸の結果や精度について、チェックポイントを押さえておきます。
重要な指標として、棚卸差異率、または在庫差異率、誤差率などと呼ばれるものがあります。
これは帳簿在庫と棚卸結果いわゆる実在庫のギャップを表す指標です。
100の帳簿在庫を、棚卸で数えてみたら105個あった、
と言う場合は、差異率5%となるわけです。
会社によりますが、一般的には3%以下、悪くても5%以下に収まっているのが理想とされています。
◆棚卸差異が発生する要因
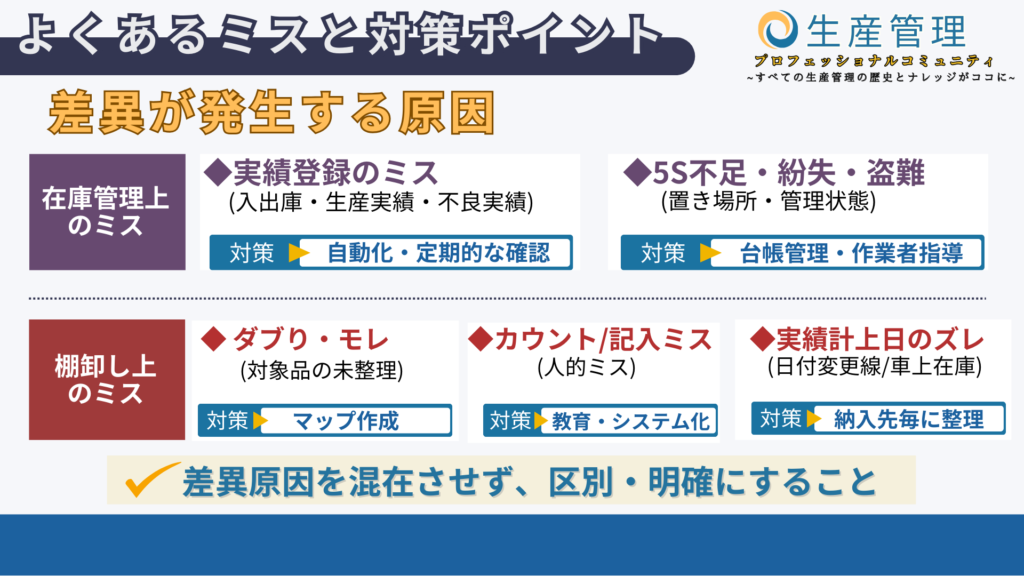
差異が発生する要因は、
普段の在庫管理上のミスと棚卸をした際のミスという2種類が存在します。
在庫管理上のミスと言うのは、入出庫や生産実績、
不良実績を登録する際にミスをしている場合です。
過剰に計上したり、処理をし忘れていると、帳簿在庫とずれてきてしまうので、
ヒューマンエラーが出ないように自動化したり、定期的な確認によって未然に検知できる仕組みが必要です。
他にも、置き場所が不明確だったり、もしかしたら紛失や盗難の可能性もあります。
きちんと台帳を管理したり、現場作業者への教育をして防いでいきましょう。
こういった、普段の管理はしっかりしていても、
棚卸当日にミスによって差異率が大きくなることもあります。
よくあるのは、棚卸を重複してカウントしてしまったり、モレてしまうケースです。
棚卸の差異には、何がどこにあるのか、
誰が、いつカウントするのか、棚卸マップやスケジュールを作成するのが重要です。
また、人が数えていると、数え間違えてしまったり、
記入ミスによって、差異が発生する場合も多いです。
数を数えることや正しく数字を書くということは、
一見簡単そうですが、やってみるとどうしてもミスは発生します。
しっかりと教育することも大事ですが、
できるだけシステム化してヒューマンエラーを防いでいきましょう。
そして、大きな際につながりかねないのが、実績計上日のズレです。
すでに出荷処理がされているのかどうか、輸送中のものの扱いはどうするのか、
日付変更線やそのあたりのルールを徹底して、全員周知しておかなければ、
棚卸すべきものが漏れてしまったり、その反対も発生する可能性があるわけです。
こういったように、棚卸はただ数えれば良いのではなく、
普段の管理状態や棚卸をする中で起きたことへの振り返りや改善も重要であると覚えておいて下さい。
まとめ
本日のまとめです。
生産管理にとって、棚卸は一大イベントで、
その忙しさから忘てしまうかもしれませんが、在庫状況や普段の管理方法を見直す絶好のタイミングです。
ぜひ、その目的を忘れずに、効率的で効果的な棚卸を実施できるようにしていってください。
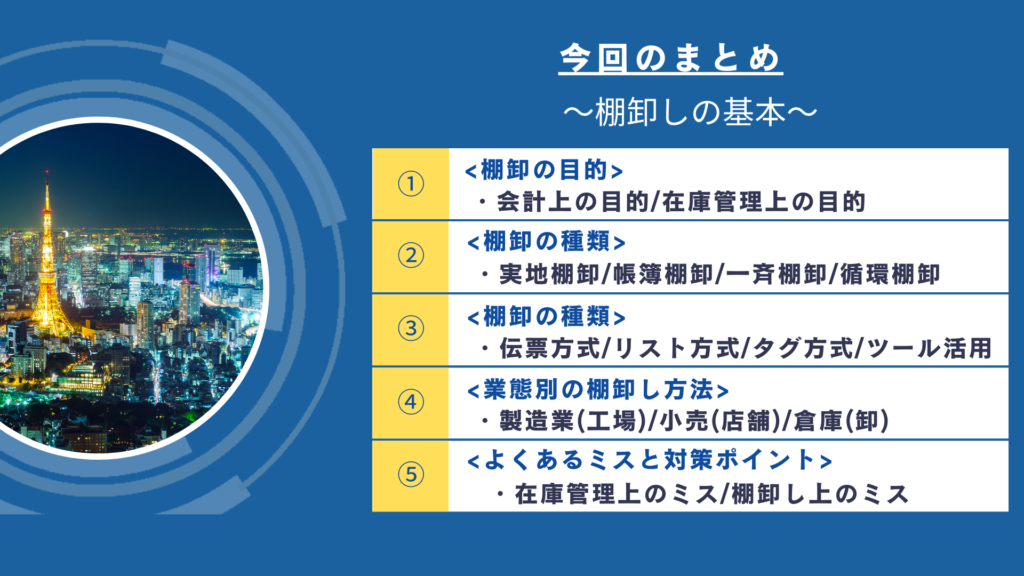
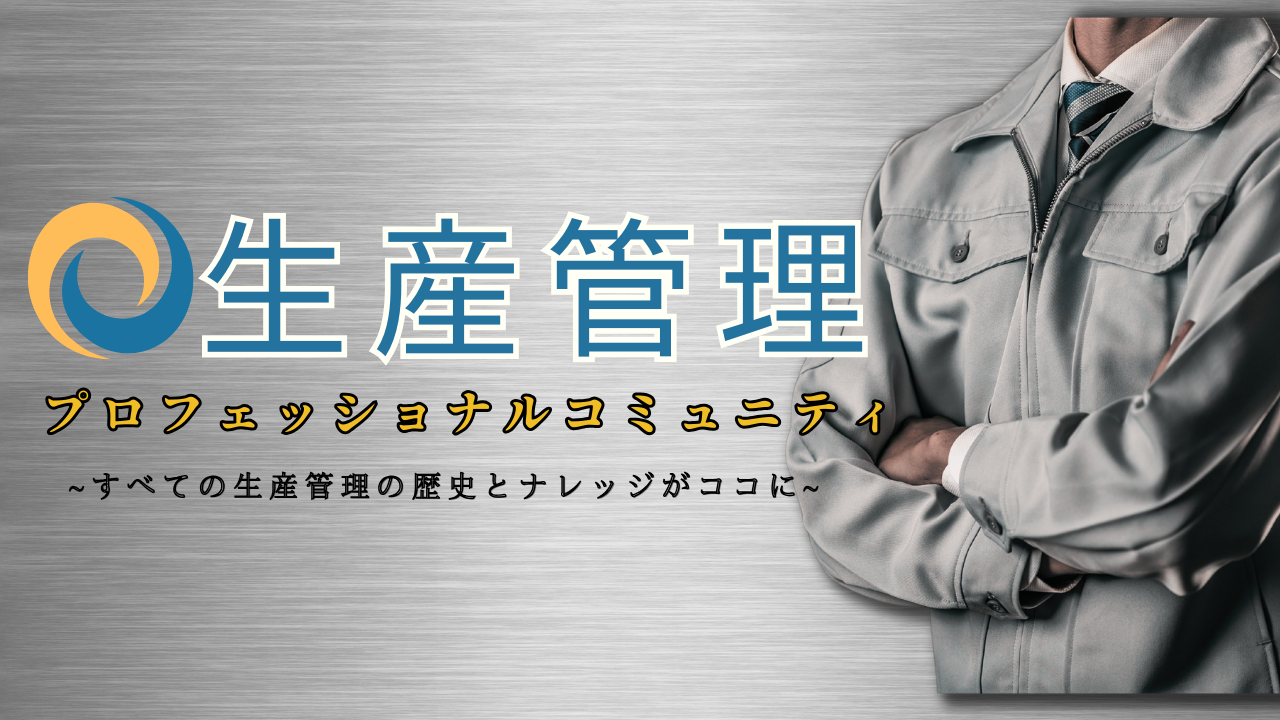
コチラのコラム記事は
ほんの一部分に過ぎません!
『生産管理プロフェッショナルコミュニティ』に入会すれば...
✅すべての教材テキストを見放題!
✅疑問・質問・悩みをいつでも相談し放題!
✅生産管理の精鋭と交流でき、成長し放題!