工場の安全対策とは?
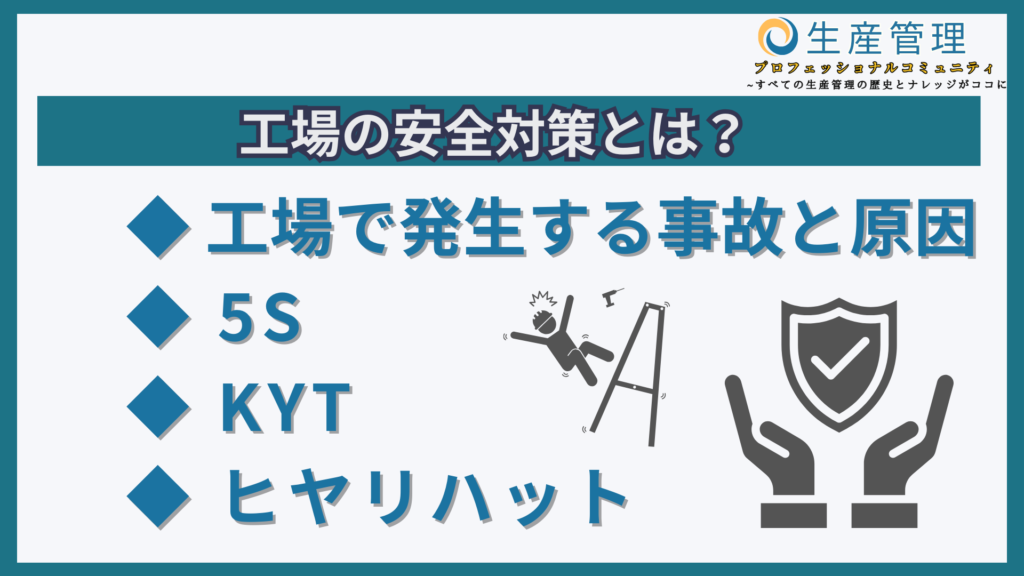
工場の安全対策は、
作業員の安全を確保するために行われる重要な取り組みです。
安全対策の目的は、労働災害の発生を回避し、
作業員の事故やケガを防止することにあります。
製造業では、ヒューマンエラーや設備に起因する危険が潜んでいるため、
安全対策は欠かせません。
工場で安全対策を徹底する目的は、
労災事故を未然に防ぎ、ケガ人や死亡者を出さないためです。
工場には、人間による機器の操作ミスや設備不良など危険が潜んでいるので、
きちんと理解して未然に防いでいける体制を築いていきましょう。
目次
工場における典型的な事故と原因
◆転倒
転倒は、体を強く打ち大ケガにつながる恐れがある事故です。
本人の不注意や作業環境の問題が原因となることがあります。
事故を未然に防ぐためには、
作業員の安全意識の向上とともに作業環境の改善や安全対策を徹底していくことです。
◆挟まれ・巻き込まれ
工場における挟まれ・巻き込まれ事故は、
重傷を負うケースがあります。
挟まれ・巻き込まれの事故の原因は、
機器の整備不良やヒューマンエラーなどです。
作業員が機器に手や体を近づけてしまったり、
機器の部品が飛び出してきたりすることで、
手や足が挟まれたり、体が巻き込まれる事故が発生しやすくなります。
事故を防止するためには、
作業効率を下げることなく機械と人の間に十分なスペースを確保することが必要です。
◆転落・墜落・踏み外し
高所からの転落や墜落、段差や階段からの踏み外しなどがあります。
特に高所からの転落はケガをするだけでなく、死亡する恐れもあります。
転落・墜落・踏み外し事故の原因は、
足場や安全柵の不備、段差の存在、作業員の不注意などです。
たとえば、足元が不安定な状態での作業や周囲の確認が
不十分な場合などに生じやすいでしょう。
事故を防ぐためには高所での一人作業を禁止することや、
高所作業時はヘルメット着用を義務付けるなどの対策を行います。
高所作業をする場合には、
作業場所の工程を管理する職長など
役職者への相談と報告を義務付けるなどのルールを徹底することも大切です。
◆切れ・こすれ
切れ・こすれ事故は、切り傷や、すり傷につながり、
作業員に被害をもたらします。
事故の原因の多くは、
カッターナイフの誤った使用や回転する刃物に誤って触れること、
道具や設備に体をこすってしまうことです。
たとえば、カッターナイフの刃先を自分に向けて使用することや、
手元が安定しないまま設備を使用し、回転する刃物に触れ、手などを切ってしまうことがあります。
切れ・こすれ事故を防ぐためには、
耐切創性手袋 の支給や、
カッターナイフの使用ルールを整え、
設備にカバーをかけることが重要です。
また、冬は作業前に手のひらを温め、作業中は手を固定する道具の使用も効果的です。
事故防止のためには、作業員に適切な研修や安全教育を行い、
作業現場を見守る上司の目配りも欠かせません。
◆感電事故
感電事故によって重度の火傷や意識不明、
心臓停止などの重傷を負うことがあり、場合によっては死亡するケースもあります。
感電事故の原因は、不適切な配線、
保護装置の欠陥、電気機器の故障、作業者の不注意や慢心などです。
感電事故は、直接触れた場合のほか近くにある導体に手を触れるだけでも起こり得ます。
また、電気の接地が不十分な場合や、
電気によって火花が飛び散る場合も事故につながる可能性があります。
感電事故を防ぐためには、適切な配線と保護装置の設置、
電気機器の点検、作業者の正しい知識と技能向上、そして安全対策の徹底が必要です。
5S
5Sとは、職場の改善活動に使用される手法の1つで、
整理・整頓・清掃・清潔・躾(しつけ)の頭文字をとって名付けられたものです。
5Sに工場が取り組む目的は、生産性や、安全性、品質などの向上です。
◆整理
5Sにおける整理の目的は、事故の原因を取り除くことです。
工場内を整理することにより工場から危険を排除できます。
たとえば、作業台付近に散らかった工具や資材、
作業途中で放置された製品などは、事故の原因になりやすいのです。
整理の実践は、不要なものの廃棄が重要になります。
◆整頓
5Sにおける整頓の目的は、作業場や倉庫内のものを整理して、
必要なものをすぐ使えるようにすることです。
必要なものをすぐに取り出せることで無駄な時間を省けます。
たとえば、部品を収納する棚やラックを整理し、
部品の種類や数量に応じて配置することで、必要な部品がすぐに手に入るのです。
必要なものがすぐに手に入るようになると、無駄な動きを省けます。
◆清掃
5Sにおいて清掃の目的は、機械や設備の異常や不具合の早期発見です。
清掃によって汚れを取り除き、
機械や設備の点検を定期的に行うと、
問題を早期に発見・解決できます。
たとえば、通常よりも切削油が多く消費されている工程では、
設備が破損して油漏れを生じていることがあるのです。
常に清掃が行き届いている職場では、異常がすぐに発見できます。
また、ホコリなどのゴミが製品に付着しにくくなるので、
品質異常の発生防止にもなるのです。
◆清潔
5Sにおける清潔とは、3S(整理・整頓・清掃)が
標準化されているかどうかです。
3S(整理・整頓・清掃)が徹底できており、
業務に必要なものがいつでも取り出せる状態の保持が「清潔」です。
◆躾(しつけ)
躾(しつけ)の目的は作業員への教育です。
ルールや規律を守り、決められたことを実行できるように教育して習慣づけます。
作業における手順を守らなければ、不良品が出る恐れがあるためです。
たとえば、生産ラインでは、
正しい作業手順を守ることで品質の確保や作業効率の向上を図れます。
また、職場内の安全管理においても、ルールや規則を守ることが重要です。
KYT
KYTとは「危険(Kiken)予知(Yochi)トレーニング(Training)」のことです。
KYTの目的は、訓練を行って作業員自身が危険を予知できるようにすることです。
KYTでは、作業状況を表したイラストシートを使うことがあります。
イラストシートには、作業場所や機器の配置、
作業手順、危険箇所などが描かれている点が特徴です。
訓練の参加者らは、
イラストシートを用いながら作業中の危険について話し合うことができます。
KYTの実施によって、作業員が慎重に作業を行うようになるため、
安全性が高まる効果を期待できるでしょう。
ヒヤリハット
ヒヤリハット
「ヒヤリハット」とは、重大な事故につながりかねない出来事を指します。
たとえば、工場内で歩行帯の白線が引かれていなかったため、
フォークリフトに作業員が撥ねられそうになったケースがヒヤリハットです。
工場で働く作業員が、
思わずヒヤリとしたことやハッとした出来事をヒヤリハットと呼びます。
ヒヤリハットを全作業員で共有、改善策を検討し、
重大な事故の防止を目指すことが重要です。
ヒヤリハットで済んだ出来事でも、
次は重大な事故につながる恐れがあります。
ヒヤリハットの共有によって、
ほかの作業員も同様のリスクに気づけるため、事故防止が期待できるのです。
おわりに
様々な危険物を扱う工場では1つの事故が命に関わることもあり、
安全を守るためにルールの厳守を徹底しなければなりません。
安全対策を「行いすぎる」ということはありません。
作業員全員が安心して働ける工場にするために、日々実践していきましょう。
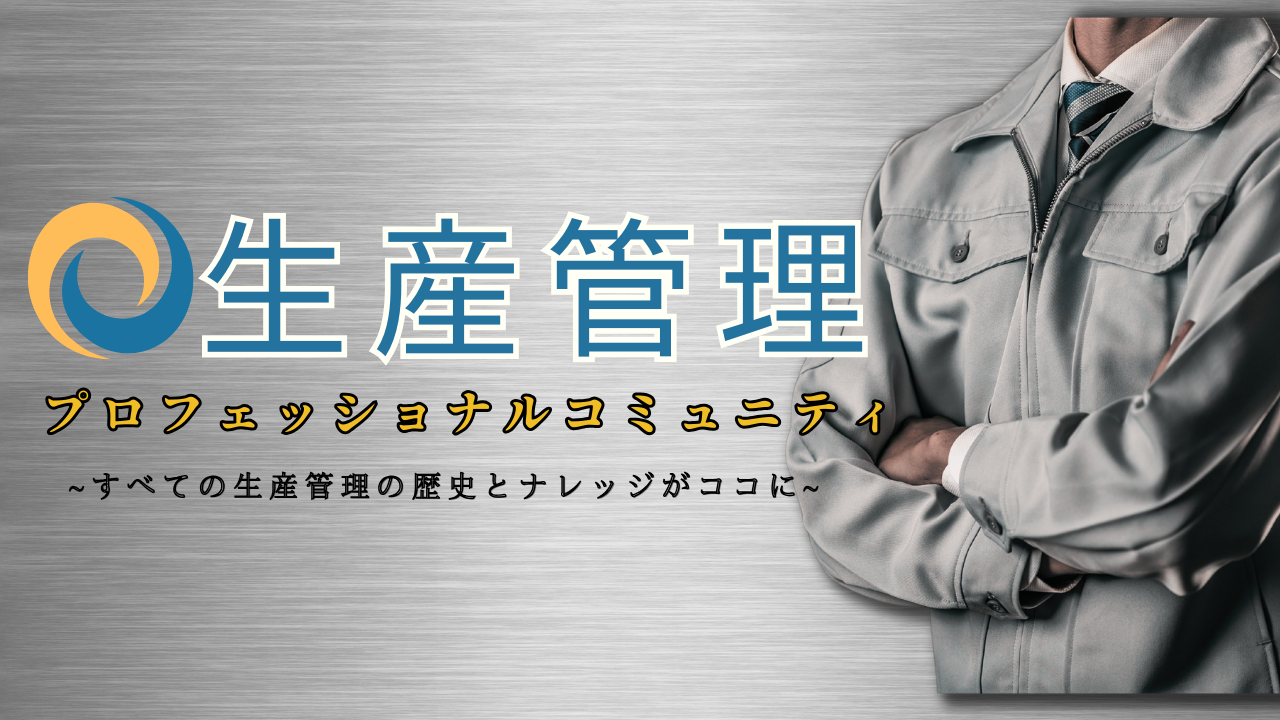
コチラのコラム記事は
ほんの一部分に過ぎません!
『生産管理プロフェッショナルコミュニティ』に入会すれば...
✅すべての教材テキストを見放題!
✅疑問・質問・悩みをいつでも相談し放題!
✅生産管理の精鋭と交流でき、成長し放題!