在庫とは?在庫管理の目的は?
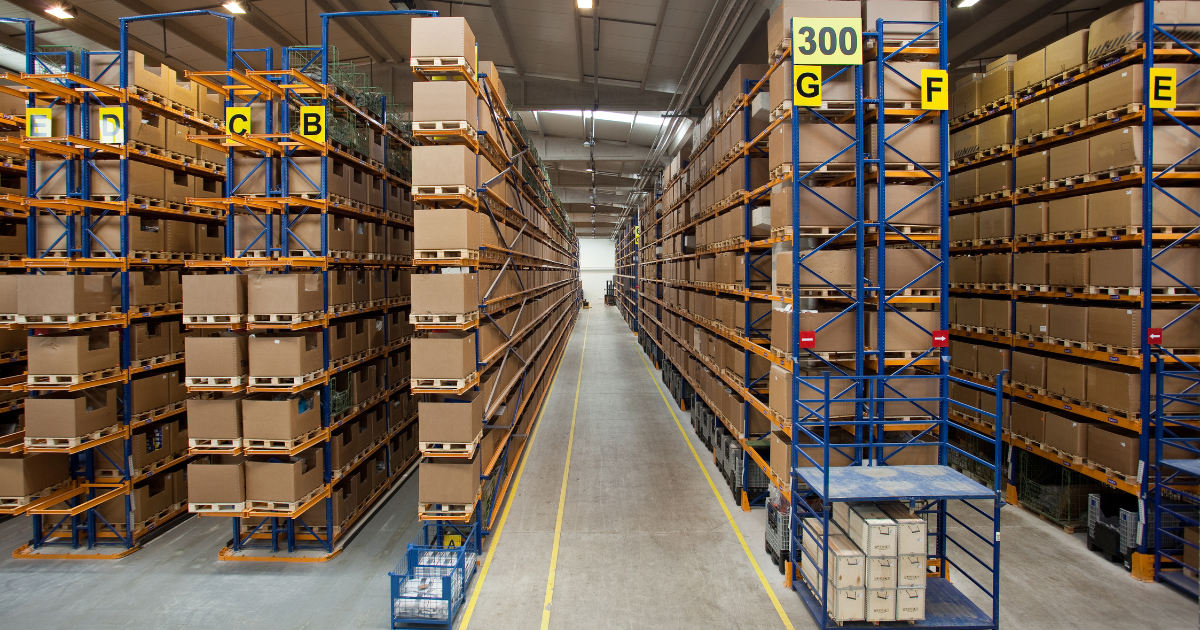
生産管理をしている多くの人が抱えているのが在庫の問題です。
在庫管理の難しさや重要性は誰もが理解していますし、
在庫を適正にコントロールすることこそが
生産管理の最も重要な任務の一つともいうことができます。
分かっているつもり、
やっているつもりになってしまっている人であっても、
一流の生産管理パーソンになりたいのであれば、
在庫管理について理解を深めていただきたいと思います。
目次
在庫とは?
在庫には、大きく分けて3種類に分けることがあります。
(資産管理上や会計上はさらに細かく分類することもあります)
簡単に言うと、仕入れたモノ、加工途中のモノ、完成したモノの3つです。
それぞれについて見ていきましょう。
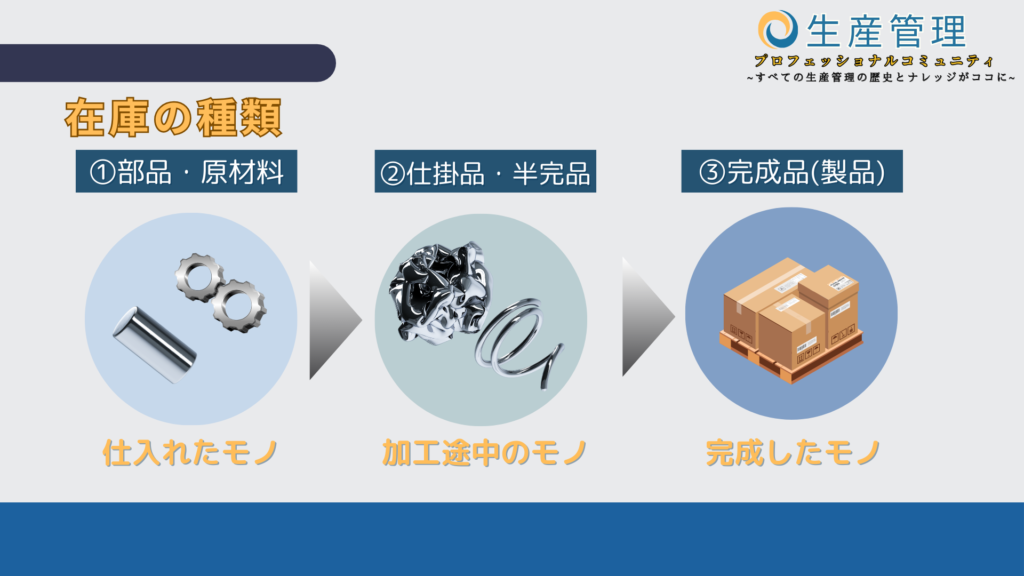
①部品・原材料(素材)
部品・原材料とは、外部業者から仕入れて、
素材として製品を作るのに用いられる在庫のことです。
鉄材や樹脂材などの加工しなければ使えない
「原材料」の在庫と、
ねじやナットなどのすぐに使える1つの製品である
「部品」の在庫があります。
また、部品・原材料を発注してから納品されるまでの時間(日数)を
「調達リードタイム」や、
「発注リードタイム」と呼びます。
このリードタイムによって
在庫の量をコントロールしていくわけです。
発注してもすぐに入荷しないものは在庫を多く抱える必要がありますが、
発注してすぐに入ってくるものは最小限の在庫で済みます。
こういったように、発注リードタイムに合わせて
必要な量を調達していくことが重要です。
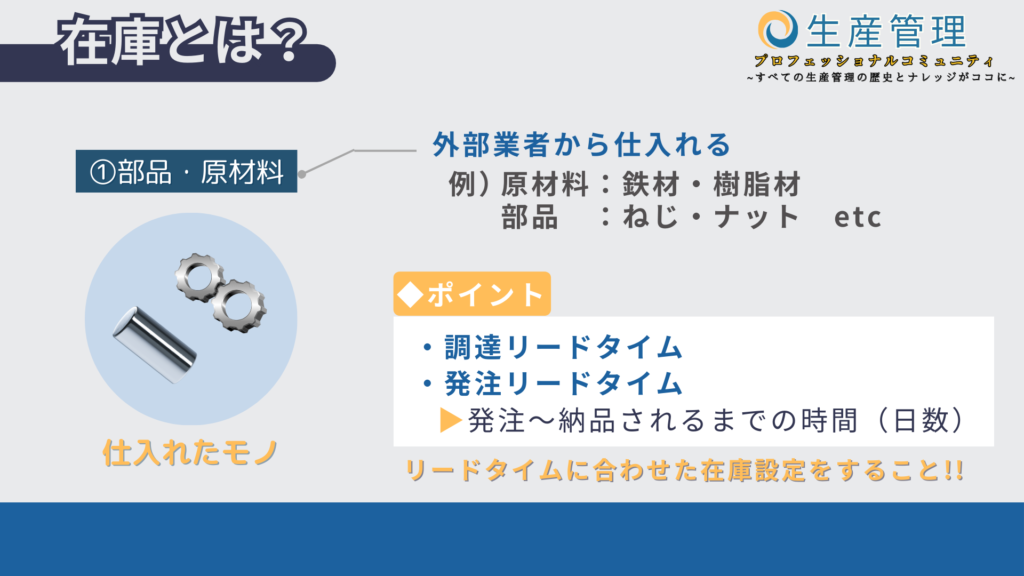
②仕掛品・半完品
原材料と部品を加工したり、
組み立てたりして最終的な製品を生産する過程で
作られる途中のモノを仕掛品と言います。
例えば、小麦粉という原材料を使用して作られたものの、
まだ焼かれていないパンの生地が該当します。
パイプを切っただけで、加工途中であったり、
組付け部品を装着する前の状態も該当します。
また、中間的な生産物として、
製品自体は完成されているが、
販売できない状態の品物を「半製品」といいます。
例えば、ラベルが貼られていないや品質チェックをする前の製品などが挙げられます。
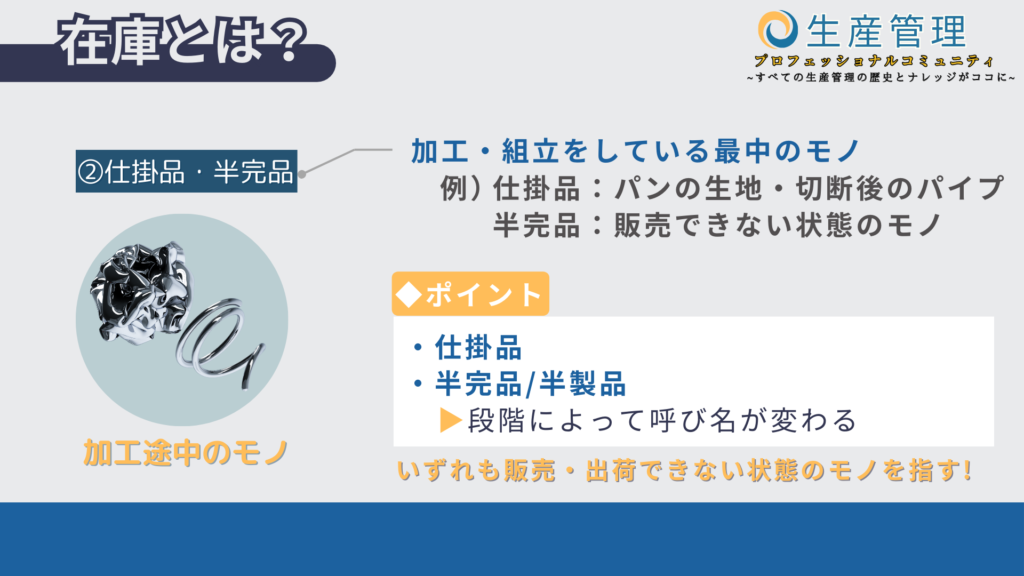
③完成品(製品)
焼かれたパンや組み立てたノートパソコンのように、
仕掛品を経て完成する、
顧客に販売できる状態の在庫が「完成品(製品)」です。
完成品の在庫は、
自社の工場の中だけに存在するのではなく、
小売店に並んだり、客先に届けられたりする
というのが材料や仕掛品との違いで
上記の①の部品や材料に対して、
②の過程で加工をする人件費や材料費、
さらには完成したときに発生する付加価値によって、
工場内にあるモノの中で資産価値が高い状態です。
資産価値だけではなく、
スペースとしても①②に比べて大きくなるケースがほとんどですので、
最少限の在庫に留める工夫が必要です。
会社内、工場内にある在庫の種類を押さえ、
適切な在庫管理に役立てていきましょう。
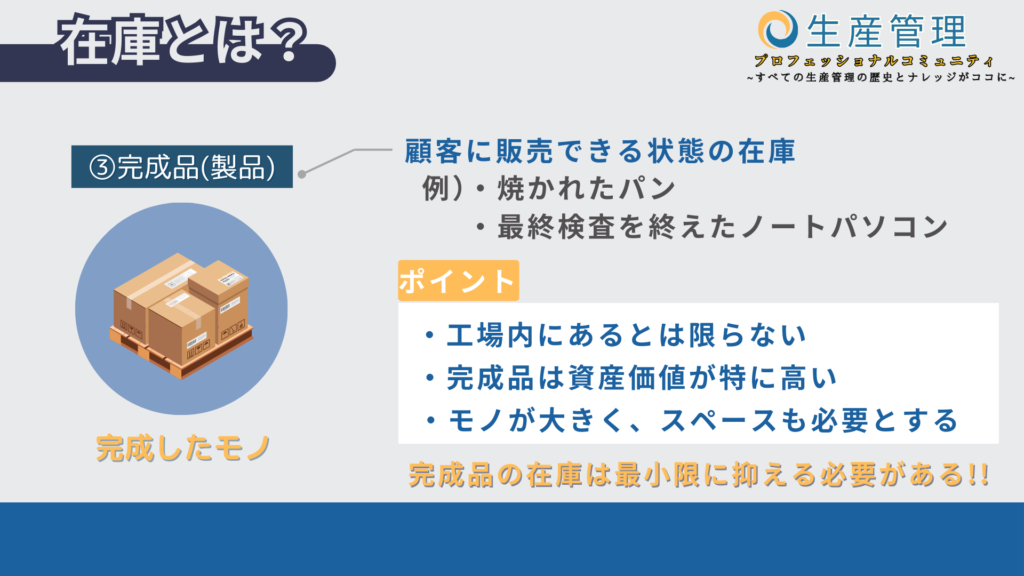
在庫管理の重要性
在庫は資金繰りに影響するので、
"在庫は悪だ"、"とにかく減らすべきだ"との考えがあります。
しかし、在庫がなければ販売や生産が滞ってしまいます。
戦略的に在庫を確保しておくべきケースは数多く存在します。
"在庫"が悪なのではなく、在庫を"コントロールできない"ことが悪なのです。
その重要性について触れていきます。
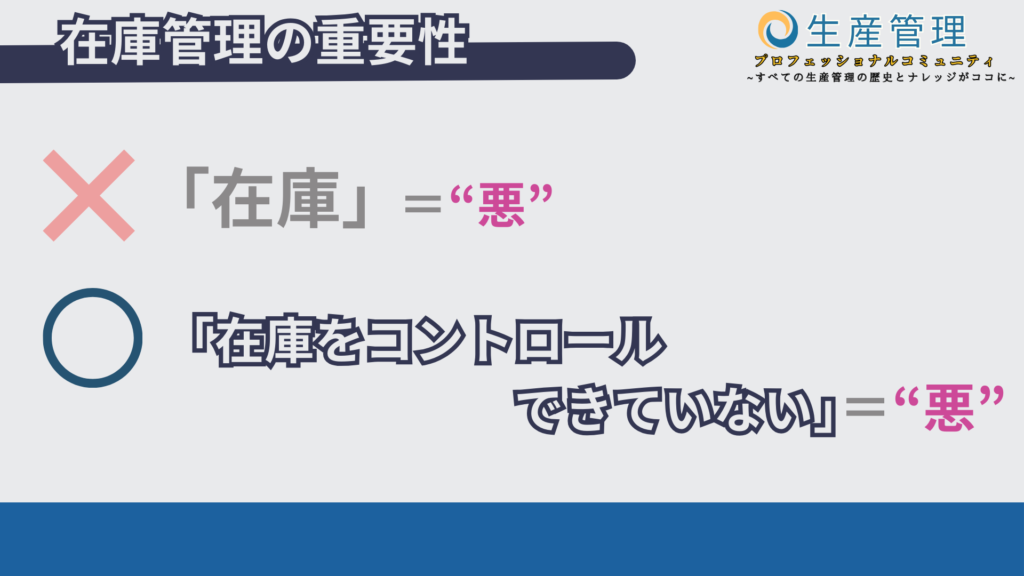
◆適正な在庫管理が工場・会社の売上利益に直結する
工場の中で必死に戦っている生産管理パーソンは
つい忘れてしまいがちですが、在庫はおカネです。
在庫が多すぎる場合、資金繰りに悪影響を及ぼしますが、
逆に少なすぎても、生産が滞り、納期が守れなくなり、
売上が立たなくなったり、
お客様に迷惑をかけてしまうことにもなり得ます。
また、スペースの問題もあります。
不要な在庫は倉庫を占有することで保管費を増大させますし、
在庫が多すぎると様々な問題が見えづらくなってしまい、
改善が進まない、という問題も発生します。
さらに、万一製品が劣化してしまったり、
もう売れなくなってしまうこともあります。
そういった事情で廃棄することになってしまった場合には
損失が発生するので、
会社の利益に悪影響を及ぼしてしまうのはイメージできるでしょう。
逆に、
適正在庫が維持できれば、
適正な生産により、生産と販売を充たし、
売上に貢献します。
資金繰りにも影響が小さくなり、
保管費 も廃棄費用も減り、利益を増大させてくれるのです。
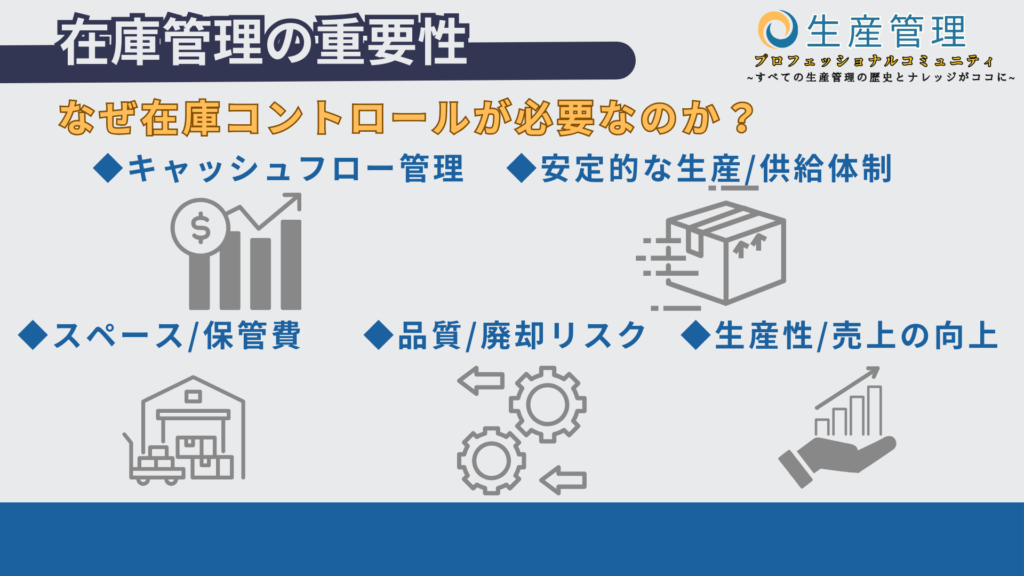
つまり、適正在庫の目的は、
工場会社の売上利益の維持増大に貢献することであると言えるわけです。
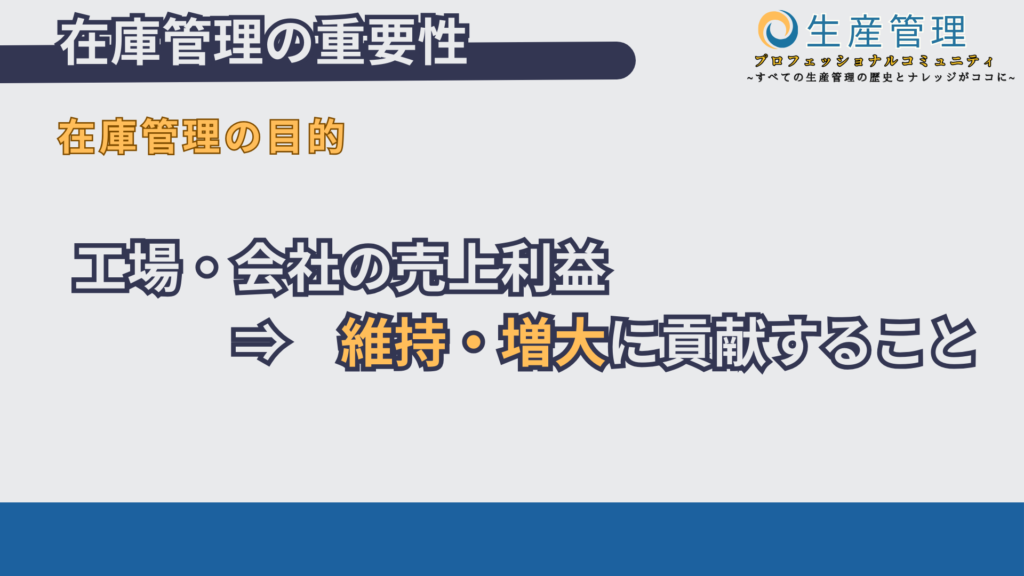
◆在庫をコントロールするとは
在庫管理のあるべき姿は
「必要なモノを、必要な場所に、必要なタイミ ングで、必要な量だけ」 揃えることです。
つまり、 成り行きで発生してしまうものではなく、
在庫が計画的に、戦略的にコントロールされていることが肝要です。
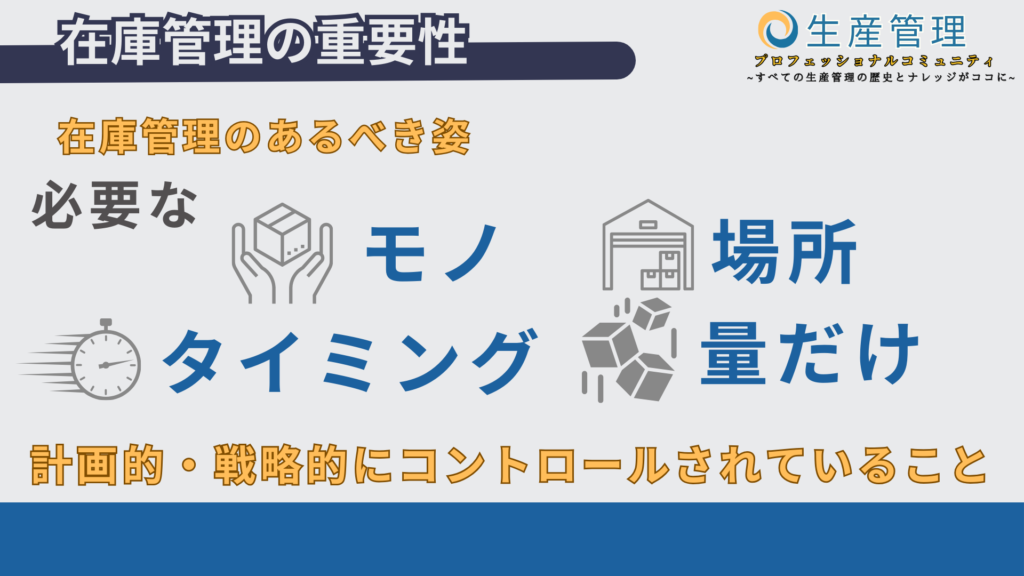
在庫は各業務の結果として発生します。
営業の販売計画が達成しない、
仕販在計画がいい加減、
生産が生産計画どおりにならない、
品質が悪く、余計に製品をつくり、部材を消費する、
納期どおりに部材が入らない。
といったことが起きると、
結果的に在庫が適正範囲を超えて増減してしまうのです。
こういった様々な要因を加味して
適正に管理するために生産管理という仕事が重要な役割を果たすわけです。
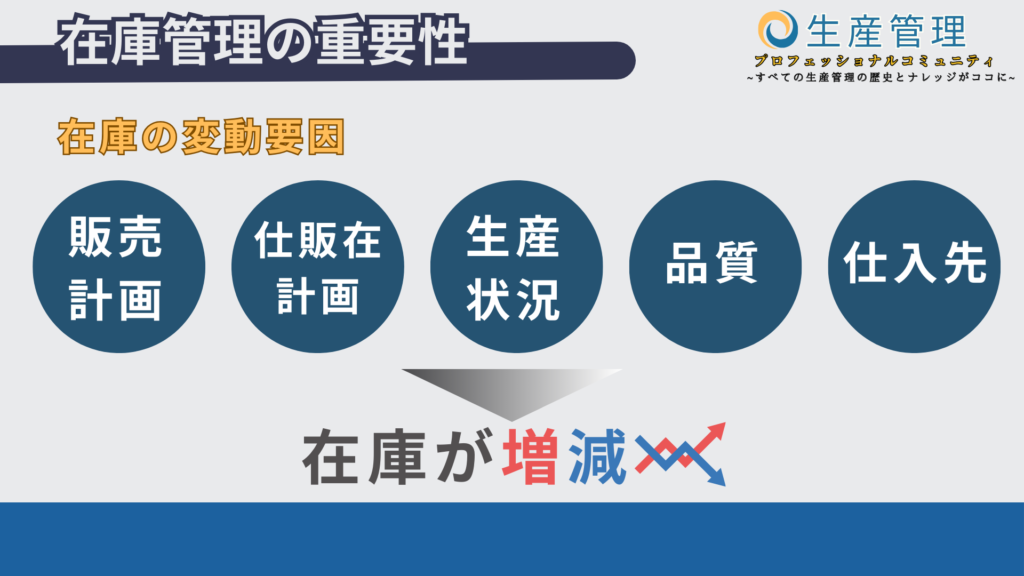
在庫はなぜ発生するのか
製造業には在庫がつきものです。
完全受注生産の形態であっても完全な無在庫の実現は難しいでしょう。
在庫はむしろ必要なものと考えるべきです。
その上で、適正に在庫量をコントロールするためには、
なぜ在庫が発生するのかを理解しておくことが重要です。
では、どのような理由で在庫は発生するのか見ていきましょう。
◆要因①:リードタイムのギャップ
“欲しい”という要求の 時間 (リードタイム) と
生産や仕入れの時間 (リードタイム) にギャップがあるからです。
調達する(つくる)のに3日かかるのに、
顧客がすぐ欲しいという場合、 在庫で対応せざるを得ません。
この要因で発生する在庫については、
各工程や物流上のムダが無いか、効率化ができないかを考え、
短い期間で調達したり生産できる体制を築くことで
改善をしていくことが重要です。
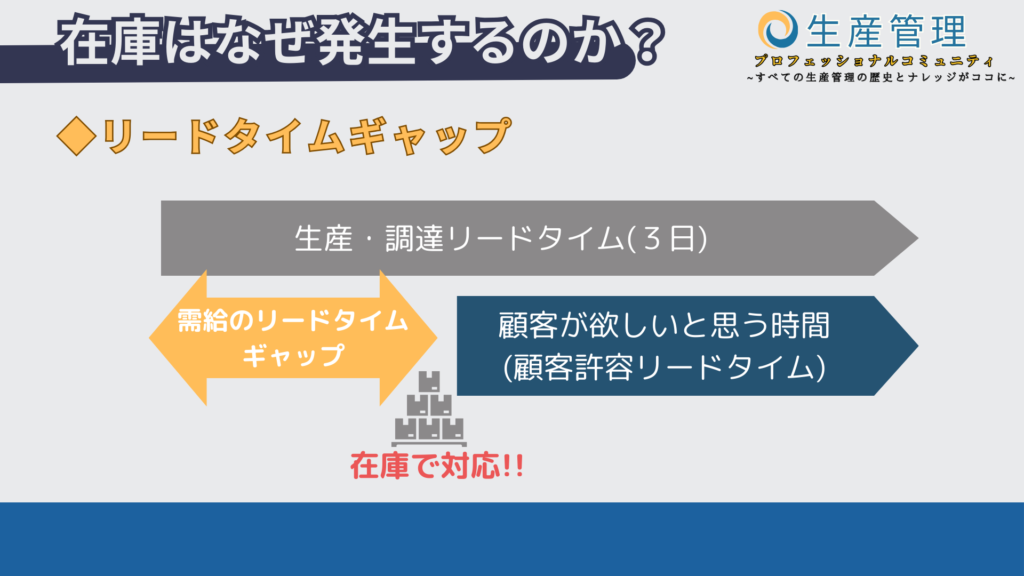
◆要因②:設備特性やロットサイズのギャップ
100個しか要らないのに、
設備の都合や、材料の都合で1000個つくらざるを得ない場合、
余分な製造分は在庫になります。
大きな設備や人件費を動かしてまで、
たった数個を生産することができない工場は多く存在します。
顧客に「欲しい」と言われれば作らざるを得ませんが、
こういった状況や事情を双方で理解しておくことが重要です。
状況によっては発生する余剰在庫の扱いや、
余分にかかる費用を売価に反映させるなどの対策が必要になってきます。
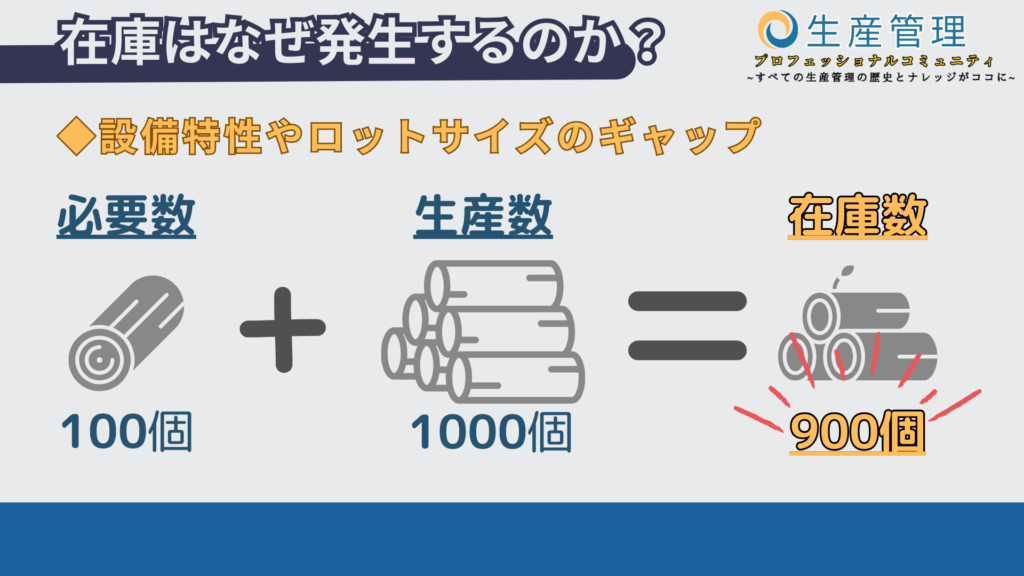
◆要因③:歩留まりギャップ
歩留まりも影響する必要があります。
100個の内3個失敗する場合、
100個 良品をつくるには 103個つくらないとなりません。
これを歩留まりといい、
歩留まり以上によくできてしまうと余計な在庫になるのです。
失敗を見越して多めに作る必要があるケースも往々にしてよくあります。
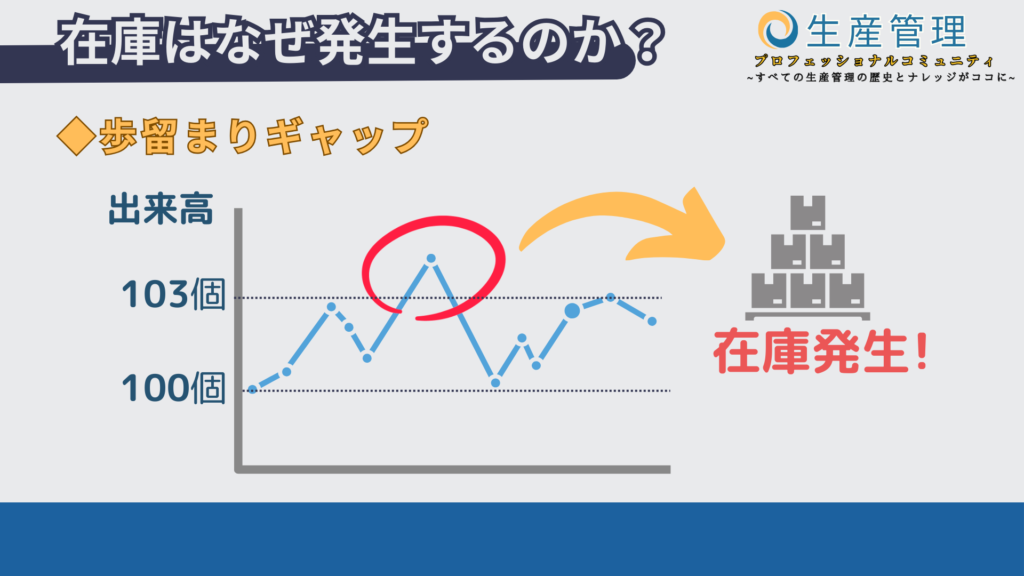
◆要因④能力ギャップ
需要量と供給能力にギャップが生まれる場面も
在庫をもつことで対処するケースがあります。
5月末に1000個まとめて納入する必要があるが、
ひと月に500個しか生産できない状況であれば、
4月・5月の2か月間で500台ずつ生産する必要があります。
そのため、4月に生産した500個は1か月間在庫として管理が必要になってきます。
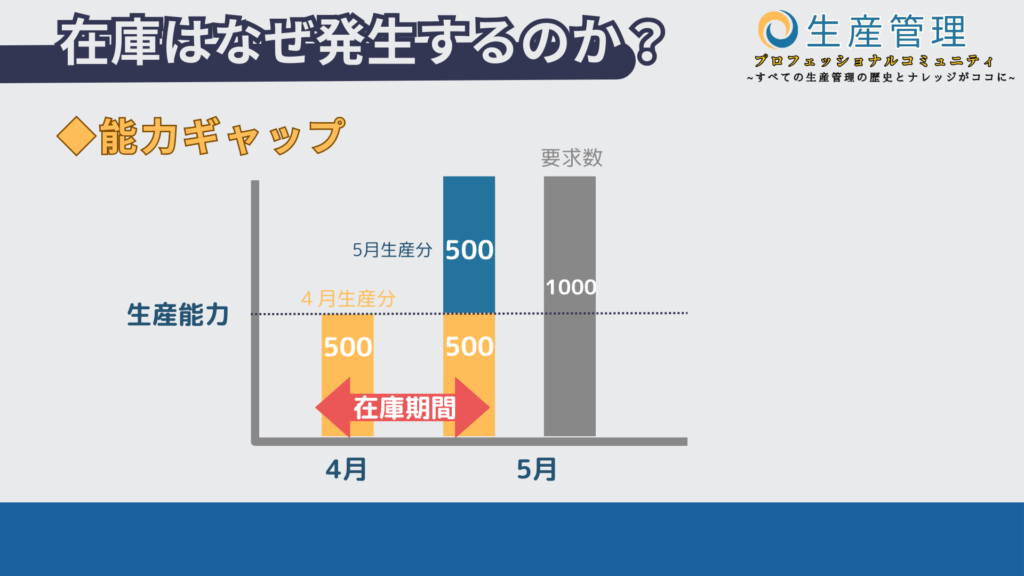
◆要因④能力ギャップ
あらゆる事情で在庫を抱えざるを得ない状況が発生します。
年度末に在庫を積み上げたり、
逆に下げたり、キャンペーン用に在庫を積んだり、
リスクに備えて在庫を抱えて置いたり、
設備を改造するために一時的に在庫を積み増したり、
会社の事情やポリシーのよって在庫が増減するものです。
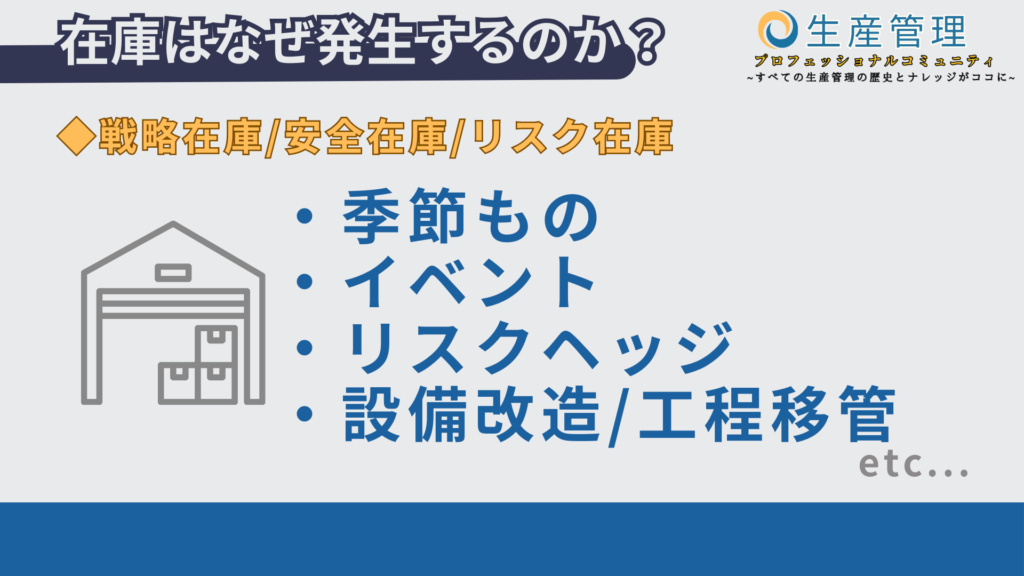
製造業が抱える在庫管理の主な課題と対策
生産管理をしている人であれば在庫管理の重要性は痛いほど理解しています。
適正化したいと思っている人がほとんどでしょう。
ですが、自信をもって適正化できている、と言える現場は多くはないと思います。
その主な要因と、とるべき対策について解説していきます。
◆在庫量が見えない
そもそも、自分の管理している工場や、
特定の製品の在庫が「どこに」「いくつ」あるのか、
よくわかっていないケースも良くあります。
Amazonの倉庫のような最先端の全自動倉庫であれば、
システマチックに在庫量を捉えて分析することはできます。
しかし、ほとんどの会社・工場では
数百点、数千点の部品や材料、製品を扱っている工場において、
そのすべての在庫を数値化することは非常に難しいです。
主なQRコードやRFID技術などのITツールを活用したりしながら、
入出庫管理のレベルを上げたり、
在庫管理システムの活用などが望ましいです。
会社の規模や状況、費用対効果を考えながら、
まずは「在庫の可視化」を進めることが重要です。
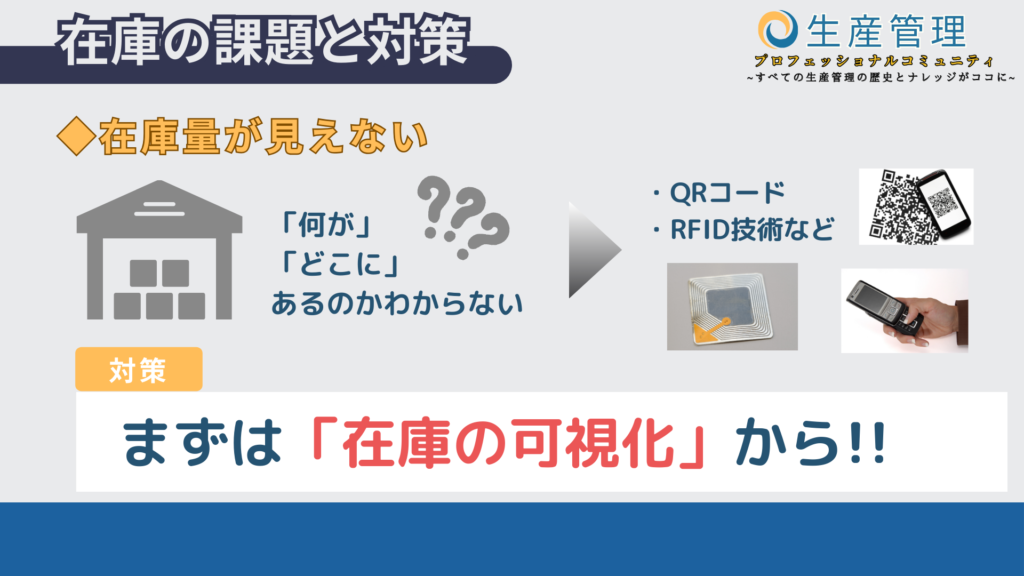
◆属人化
生産計画の作成や発注作業を、
ベテラン担当者の経験に基づいて行っている企業は少なくありません。
いつ・どのくらい生産(発注)すべきか明確な判断基準がない、
もしくは数値の設定根拠があいまいであったり、
長年見直しが行われていなかったりすることはよくあります。
また仕入品のリードタイムや出荷量の傾向、
得意先や仕入れ先の特徴など考慮すべき情報は無数にあるため、
言語化・データ化することが難しいのです。
そのため、すべての感覚や情報が担当者の頭の中にある状態です。
このように属人化した業務は客観的に評価できないため、
改善活動が進まないケースはたくさんあります。
また担当者が休みづらくなる、
担当者が変わると欠品や過剰在庫が発生する、といったリスクもあります。
在庫管理業務は複雑な業務のため、
特に属人化が起こりやすいと言われています。
こういった煩雑化してしまっている生産管理業務は
新人や若手に伝えていくことは非常に難しい課題として認識している会社も多くあります。
ベテラン担当者が経験してきたことを可能な限り言語化・数値化していくことで、
誰がやっても同じクオリティに再現できるように
マニュアルやナレッジを蓄積して標準化を図ることが重要です。
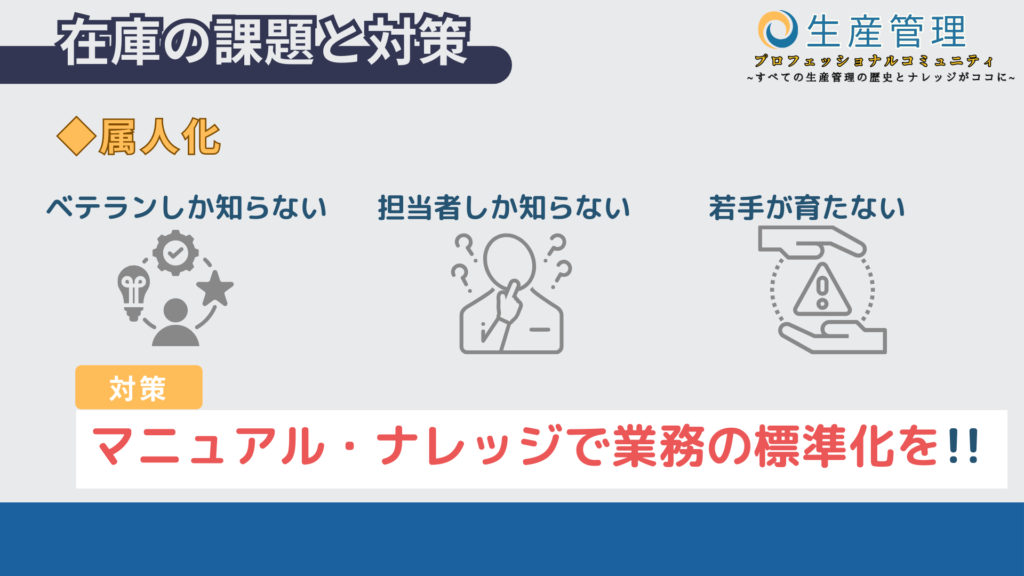
◆心理的要因
生産管理をやっている人が一番恐れていることは、
「欠品によるライン停止・納入遅延」です。
在庫が切れてしまって、生産ラインを止めて、多くの機会損失を生み出してしまうことです。
こういったことを防ぐために、在庫を多めに抱えてしまうことは頻繁あります。
無意識的にそうなってしまっている工場も多いかもしれません。
ですが、
そういった感情やコツに頼った在庫管理をしているようでは、
適切な在庫コントロールはできません。
あらゆる状況を反映して、数値で判断できる基準を設けたり、
多い・少ないの判断を客観的に判断できるようにシステムを導入する、といった対策が有効です。
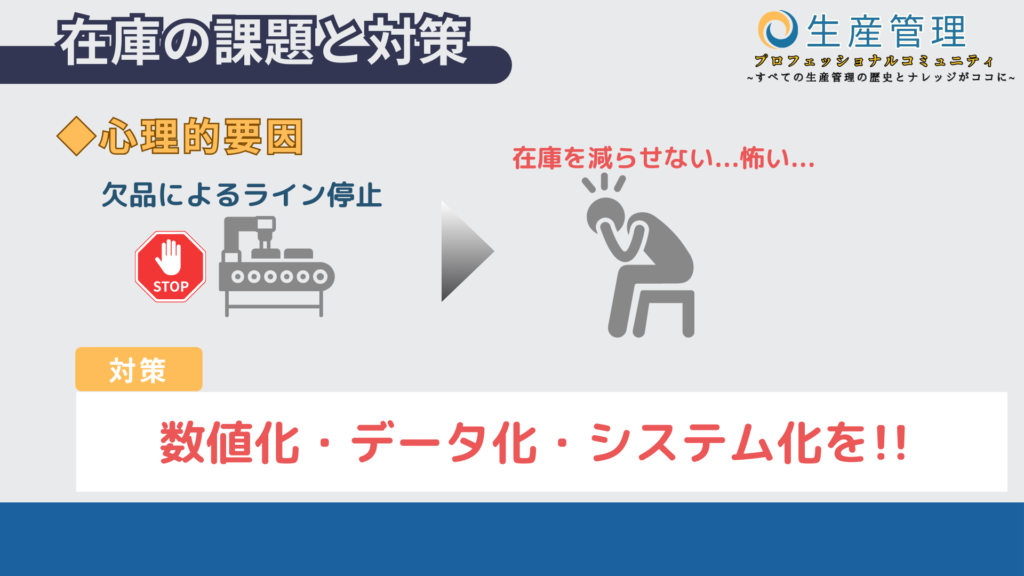
まとめ
今回、在庫や在庫管理の重要性やむずかしさについて解説をしていきました。
本当に難しい領域ですし、
正解が一つではないのも事実です。
様々な施策やシステムについて、
別記事で紹介していますので、ぜひ参考にしてみてください。
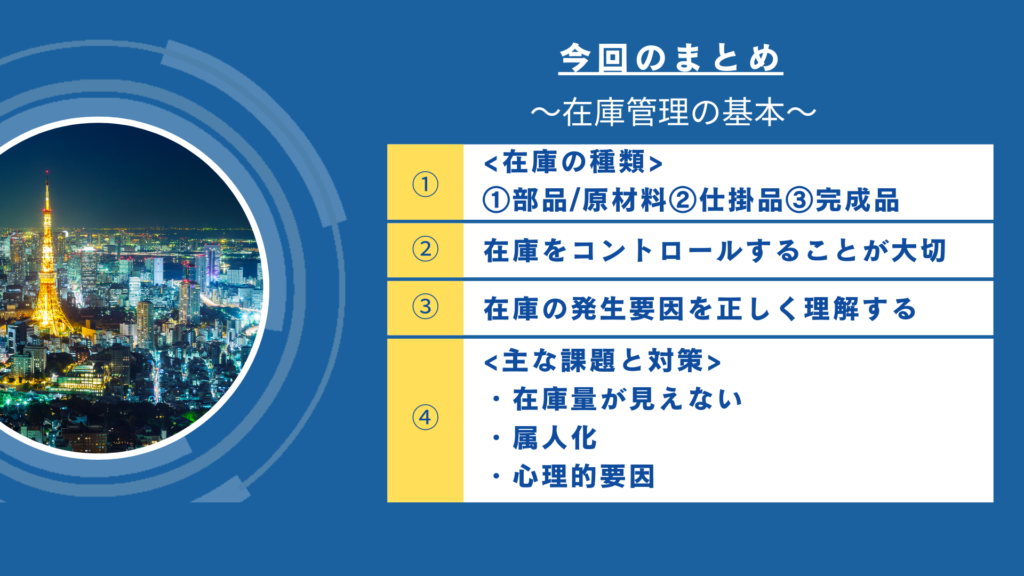
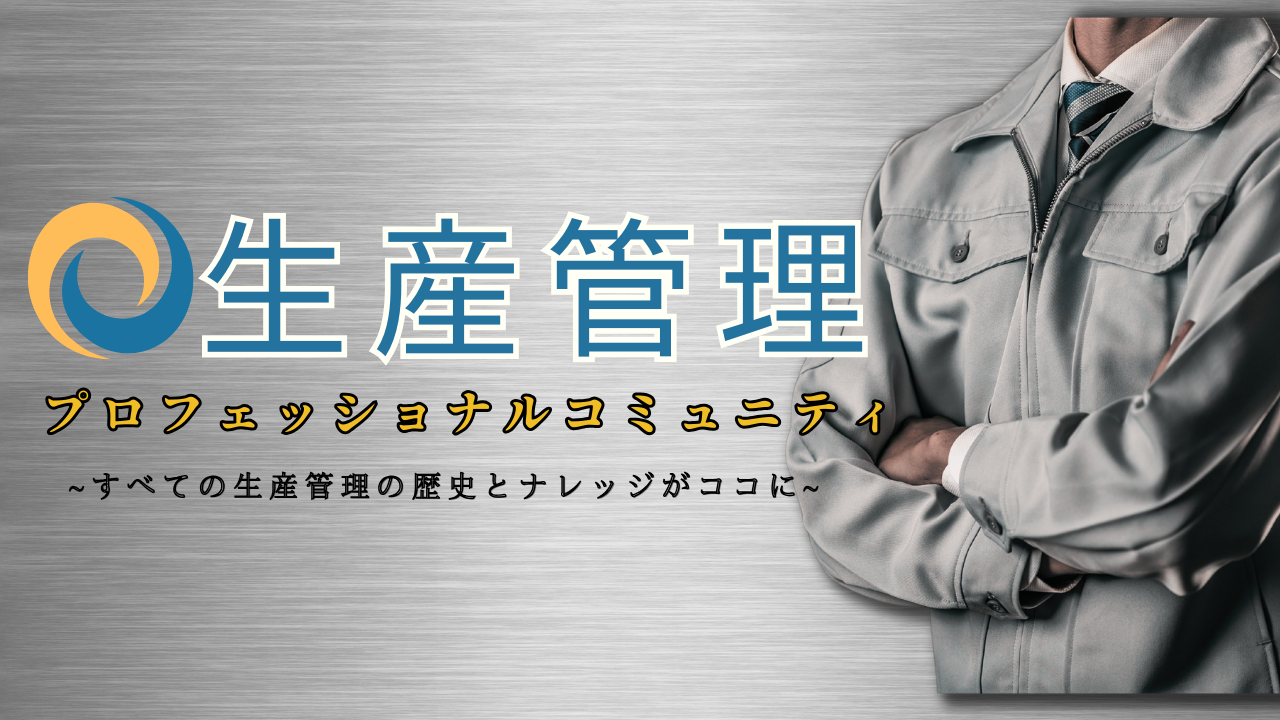
コチラのコラム記事は
ほんの一部分に過ぎません!
『生産管理プロフェッショナルコミュニティ』に入会すれば...
✅すべての教材テキストを見放題!
✅疑問・質問・悩みをいつでも相談し放題!
✅生産管理の精鋭と交流でき、成長し放題!
投稿者プロフィール
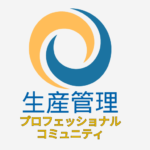